당신은 주제를 찾고 있습니까 “자동차 센서 – 108.자주나오는 센서의 역활 / 자동차정비기능사실기“? 다음 카테고리의 웹사이트 https://you.maxfit.vn 에서 귀하의 모든 질문에 답변해 드립니다: https://you.maxfit.vn/blog. 바로 아래에서 답을 찾을 수 있습니다. 작성자 콜탕티비 이(가) 작성한 기사에는 조회수 4,855회 및 좋아요 52개 개의 좋아요가 있습니다.
자동차 센서 주제에 대한 동영상 보기
여기에서 이 주제에 대한 비디오를 시청하십시오. 주의 깊게 살펴보고 읽고 있는 내용에 대한 피드백을 제공하세요!
d여기에서 108.자주나오는 센서의 역활 / 자동차정비기능사실기 – 자동차 센서 주제에 대한 세부정보를 참조하세요
Created by VideoShow:http://videoshowapp.com/free
자동차 센서 주제에 대한 자세한 내용은 여기를 참조하세요.
자동차 센서 정리 – 네이버블로그
대기압센서(BPS)는 공기유량센서(AFS)에 부착되어 자동차가 위치한 지역의 대기압력을 측정해 ECU로 신호를 보낸다. ECU는 이 신호를 이용해 차의 …
Source: blog.naver.com
Date Published: 4/11/2022
View: 7142
자동차용 센서 시스템 IC 기술개발 동향 및 고신뢰성 이슈
현재의 자동차용 센서 들은 자동차의 각 시스템에 신경망처럼 분. 산 배치되어 차량의 상태를 실시간으로 파악하고 검지하여주는 핵심. 적인 기능을 하고 있다. 또한 …
Source: www.koreascience.or.kr
Date Published: 6/17/2022
View: 8416
자동차 센서
E-mail: [email protected] http://web.yonsei.ac.kr/hgjung. 내용. • 센싱의 원리. • 자동차용 센서. • MEMS 기술. • 센서 네트워크 …
Source: web.yonsei.ac.kr
Date Published: 7/22/2021
View: 9149
자율주행차, 사람보다 안전한 운전 비밀은 ‘센서 3형제’에 있다
차량 내 인공지능(AI) 컴퓨터(PC)는 센서에서 수집한 정보로 차량을 제어한다. 이 제어기가 자동차의 각 부품에 명령을 내리면, 마치 인간이 두 발로 움직 …
Source: www.hankookilbo.com
Date Published: 6/3/2021
View: 6783
자동차용 센서 시장 – 연구개발특구진흥재단
라이다(LiDAR) 제공업체와 다양한 자동차 관련 업체의 합작 투자 증가. 및 센서 융합으로 인해 자동차 센서의 사용이 증가함에 따라 예측 기간. 자동차 센서 업체의 …
Source: www.innopolis.or.kr
Date Published: 3/17/2021
View: 8599
주제와 관련된 이미지 자동차 센서
주제와 관련된 더 많은 사진을 참조하십시오 108.자주나오는 센서의 역활 / 자동차정비기능사실기. 댓글에서 더 많은 관련 이미지를 보거나 필요한 경우 더 많은 관련 기사를 볼 수 있습니다.
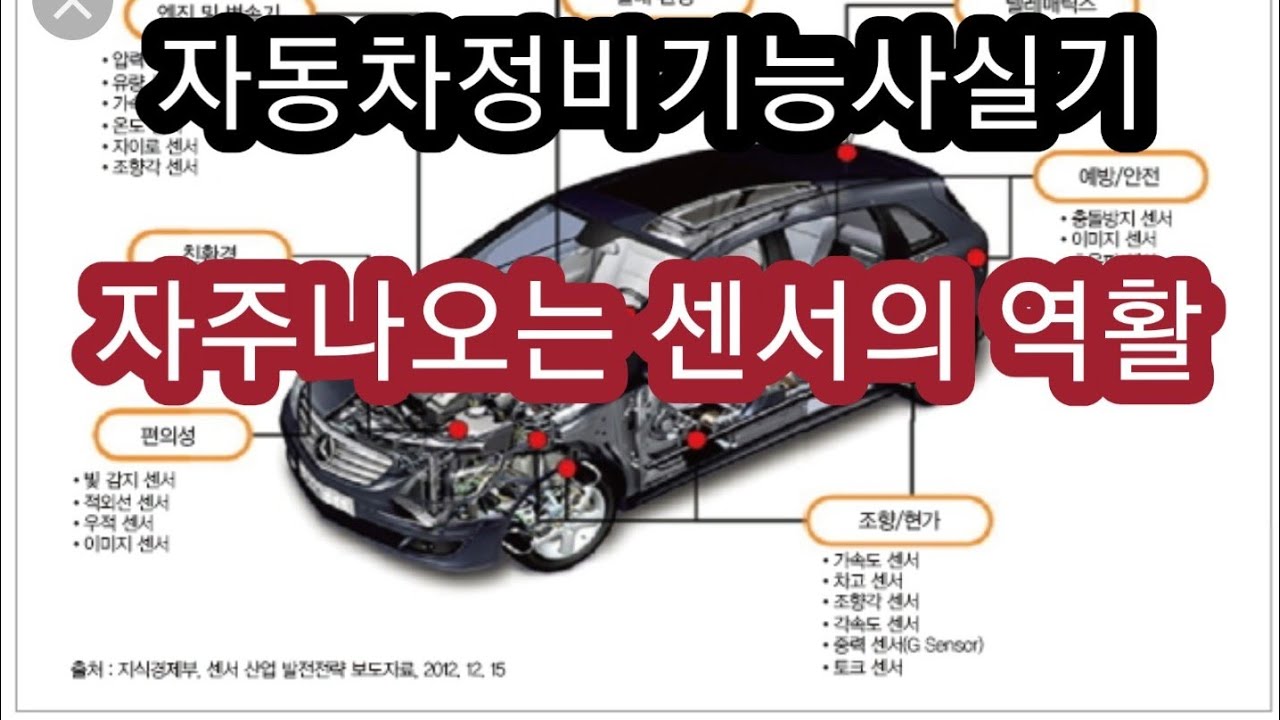
주제에 대한 기사 평가 자동차 센서
- Author: 콜탕티비
- Views: 조회수 4,855회
- Likes: 좋아요 52개
- Date Published: 2019. 5. 24.
- Video Url link: https://www.youtube.com/watch?v=7EDT3KY-2-U
차량용 센서
차량용 센서는 자동차에 탑재되어 차량 내외부 정보를 감지 또는 측정하여 전기적인 신호로 변화하는 장치이다. 차량용 센서는 기계, 전자, 통신, 제어 기술들과 융합하여 자동차의 안전성과 편의성을 획기적으로 향상시킬 수 있는 전자제어 시스템의 핵심부품이라고 할 수 있다. 엔진제어 부분에서 차체자세제어를 위한 ABS(잠김방지제동장치), ESP(차량자세제어장치) 등으로 확대되었고, 에어백을 비롯한 충돌방지용 센서들이 적용되고 있으며, 편의 및 쾌적함을 위한 공조제어와 조명제어 등에 필요한 센서 적용이 점차 확대되고 있다. 최근에는 자율주행 자동차의 더 안전한 운행을 위해 카메라, 라이다, 레이다 등의 센서가 개발되고 있다.
개요 [ 편집 ]
센서란 측정 대상물로부터 정보를 감지 또는 측정하여 그 측정량을 전기적인 신호로 변환하는 장치이다. 물리량이나 화학량의 절대치나 변화, 소리, 빛, 전파의 강도를 검지·검출하거나 판별·측정하여 유용한 신호로 변환하는 기능을 갖추고 있다. 차량용 센서는 자동차에 사용되는 센서를 말하는 것으로 탑승자의 안전과 직결되기 때문에 내환경성 및 고신뢰성이 요구된다. 차량용 센서는 온도의 급격한 변화, 중력의 30배가 넘는 가속 환경, 각종 전기장치에 의한 전자파간섭(EMI) 환경에서도 정상적으로 작동 되어야 하며, 습기, 부식성 물질, 유류에 의한 손상을 받지 않도록 내식성을 가져야하는 등 까다로운 조건에 만족해야 하므로, 차량용 센서는 신뢰성의 증대, 저렴한 가격, 높은 정밀도를 갖추어야 한다. 차량용 센서는 파워트레인, 섀시, 안전 및 제어장치, 배기장치, 텔레매틱스와 같은 다양한 응용분야에서 활용되고 있다.[1]
특징 [ 편집 ]
차량제어 시스템의 기술발전 방향은 기계적인 제어시스템에서 전자적인 제어시스템으로 변화되고 있으며, 이를 효율적으로 수행하기 위해서 각종 전자전기 부품간의 시스템화, 모듈화를 비롯하여 전자부품의 집적화 등이 가속화되고 있다. 이러한 전장 시스템의 정확한 동작 및 기능을 수행하기 위해서는 자동차의 실시간 운행상태와 각종 물리량을 정확하고 정밀하며 신뢰성 있게 검지하여 정보를 엔진제어장치(ECU)에 전달하여 주는 센서의 역할이 더욱 중요시 되고 있다. 자동차에 사용되고 있는 센서들은 자동차의 열악한 환경에서도 작동해야 하기 때문에 높은 신뢰성이 요구될 뿐만 아니라 다기능, 고성능이면서 가격도 저렴해야 한다는 요구조건을 만족시켜 한다. 차량용 센서는 일반적으로 영하 40도에서 영상 125도의 범위에서 사용된다. 엔진오일 압력센서의 경우 사용 온도 범위가 영상 120도에서 130도 사이이고, 배기가스 센서의 경우는 영상 600도에서 800도의 열악한 환경과 조건에서도 견딜 수 있어야 한다. 특히, 반도체 기술의 발전은 이러한 여러 가지 요구조건을 만족시킬 수 있는 솔루션을 제공할 수 있으며, 미세전자기계시스템(MEMS)에 의해 제작된 반도체 센서들이 개발되면서 소형, 고성능, 저가이면서도 높은 품질의 센서들이 생산되고 있다. MEMS 및 나노 기술과 같은 첨단기술의 활용으로 미세가공기술과 집적회로기술이 발달되어 반도체소자를 센서로 이용하게 됨으로서 검출장치도 소형화, 고밀도화 되어가고 있으며 신호처리 및 네트워크 마이크로컨트롤러(microcontroller)가 검지부와 일체형으로 센서를 구성하고 있다. 차량용 센서에 필요로 하는 중요한 특성으로는 감도, 선형도, 안정도 및 신뢰성에 대한 높은 수준의 요구사항을 만족시켜야 하며, 신뢰성 측면에서는 온도와 진동 등과 같은 기계적인 신뢰성 뿐만 아니라 센서의 전자화에 따른 전자파 내성과 정전기 등과 같은 전자기적 신뢰성 또한 동시에 만족시켜야 하는 고신뢰성 특성이 있다.[2]
스마트 센서 [ 편집 ]
차량용 센서에서는 MEMS 및 NEMS(Nano Electro Mechanical System) 기술이 급속도로 발전하고 있어 센서 기술과 이들이 접목되면서 혁신적인 기술 발전이 전개되어 나갈 것으로 전망된다. 반도체 기술을 이용하게 되면서 센서는 더욱 소형화되어가고 있으며 대량생산에 의해 수율도 좋아져서 원가도 낮아지고 있다. 집적화 기술의 발전은 한 개의 소자에서 여러 가지 가능을 할 수 있는 다기능 소자의 출현을 가져왔다. 여러 가지의 센서 소자와 전자회로, 통신 기능 및 마이크로프로세서까지 일체화된 센서시스템 반도체 칩이 출현하면서 다기능화되고 지능화된 스마트센서는 센서시스템을 소형화하고 네트워크화함으로서 자동차의 특정 위치에 장착할 수 있도록 개발되었다. 자동차의 전자화에 따른 다양한 전기전자 시스템은 센서의 신호를 처리하는데 보다 빠른 시간처리 및 메모리가 필요하게 되었다.[3] 이러한 요구사항은 반도체 센서로의 변화와 더불어 마이크로프로세서의 스마트화를 가져오게 하는 계기가 되었다. 자동차 전자화 시스템은 센서, 마이크로컨트롤러 유닛 및 파워반도체로 구성된다. 상호관계를 살펴보면 센서가 차량 내외의 정보를 검지해서 마이크로컨트롤러 유닛으로 신호처리를 하여 네트워크를 통해서 관련 엔진제어장치에 신호를 보내면 엔진제어장치에서는 이를 분석한 후 액추에이터의 동작을 조종 제어하여 주도록 하는 경로를 구성하고 있다.[3] 반도체 기술 집적도 향상에 따라 나노 스케일에 이르는 기술이 적용되면서 기존에 불가능하던 기술이 현실화되고 있다. 가스센서의 경우 종전에는 검지한계가 수십 피피엠(ppm)이었으나 탄소 나노 튜브의 등장으로 만 배 이상 으로 검지능력을 갖추어서 수 피피비(ppb) 까지 측정할 수 있게 되었다. 차량용 반도체형 센서의 상용화는 엔진제어용 흡기압 센서로부터 시작되어, 에어백 시스템, 내비게이션 시스템, 잠김방지제동장치, 차량자세제어장치 등 주로 안전, 편의장치에 다양하게 사용되고 있다. 특히 에어백과 타이어 공기압 경보장치(TPMS)의 장착, 차체 자세 제어장치(ESC)의 일반화 등 안전성 향상을 위한 법적 의무 장착은 반도체 센서의 수요를 점차 증가시키고 있다.[2]
고신뢰성 [ 편집 ]
자동차가 안전 메커니즘, 통합시스템, 자동차 솔루션 기능들을 위해 더 많은 전자 장치들을 내장하게 됨에 따라 자동차에서 전자부품의 비중은 점차 증가하고 있다. 이러한 기능들을 구현하기 위하여 20~50개의 엔진제어장치가 사용되고 이들이 대략 70~150개의 센서를 활용해 이 모든 기능들을 수행한다. 그러므로 센서들의 신뢰성은 자동차 전체시스템에 직접적인 영향을 미친다. 차량용 센서의 신뢰성 측면에서는 다양한 센서 시스템들의 자가진단 능력이 갈수록 더 중요해지고 있다. 센서의 결함을 센서 엘리먼트에서 직접 감지할 수 있다면 엔진제어장치는 어떤 것에 대한 교정 작업을 해야 할지 결정할 수 있는 신뢰성 있는 데이터를 갖게 된다.[3] 시스템의 동작정지 및 비상동작은 안전 관련 시스템에 있어서 특히 중요하다. 차량 전장 제어시스템에 대한 분석은 이러한 부품들의 복잡성이 기하급수적으로 증가하고 있음을 보여준다. 단순한 전자제어 및 조절부품들은 보다 복잡한 IT 시스템들로 대체되고 있다. 이러한 시스템들에서는 소프트웨어 그리고 엔진제어장치들 간의 상호소통이 새로운 강조점이 되고 있다. 오늘날 차량의 개별 부품들은 10~20개의 서로 다른 데이터 버스들을 통해 상호연결 되어있다. 자동차 내의 많은 기능들이 네트워크 애플리케이션화되어 과거에 보편적이던 하나의 엔진제어장치가 하나의 애플리케이션을 구현하던 구조를 이제는 여러 엔진제어장치들 간에 공유되는 네트워크 기능들이 대체하고 있다. 이러한 시스템의 고장은 임의의 결함들에 의해 야기될 수 있다. 필요한 센서 하나가 고장을 일으킬 경우 이는 관련 엔진제어장치들의 결함 메모리들에 열 가지 이상의 상이한 엔트리들을 야기할 수 있다. 오류 코드가 이처럼 많으므로 과거보다 훨씬 더 상세한 센서 진단 정보를 제공할 필요가 있다. SSC(sensor signal conditioner) IC가 모듈 내에서 센서의 고장을 감지하거나 SSC가 외부의 결함으로 인해 제대로 동작하지 못하는 상태에 처하게 되면 엔진제어장치는 이를 알 수 있어야만 한다. SSC에서 감지 가능한 결함들은 하드 오류와 소프트 오류의 두 가지 범주로 나눌 수 있다. 하드 오류들은 SSC에서 감지되는 고장들로서, 하드웨어의 문제에 의해 야기된다. 이 경우에는 신호 컨디셔닝이 정지되고 진단모드가 가동된다. 이와는 대조적으로, 소프트 오류의 원인은 항상 분명하지도 않고 연속적이지도 않다. 이런 이유로 소프트 오류에 대한 오류 카운터가 구현되어 오류가 발생하면 카운트가 올라가고, 이 오류가 더 이상 발생하지 않으면 카운트가 내려간다. 그 결과, 소프트 오류의 메시징은 저역통과 필터를 거치고 센서는 소프트 오류가 더 이상 감지되지 않으면 정상동작 상태로 돌아간다. 이러한 모드를 임시 진단 모드(diagnostic mode)라고 한다. 이후 엔진제어장치는 중복 센서나 중요성 점검 등을 이용하여 애플리케이션이 지속적으로 신뢰성 있게 동작할 수 있을지 혹은 오류 메시지와 함께 정지시켜야 할지 여부를 결정한다. 차량용 안전 관련 센서시스템의 개발은 센서 신호 컨디셔닝 IC를 이용해 크게 단순화시킬 수 있다. 센서의 출력 신호가 거의 100퍼센트 정확함을 보장해 주는 자가진단 기능은 신호 컨디셔닝 단계 그 자체 내에서만 실현 가능하며, 이 같은 기능들은 칩 상에서 구현해야만 한다. 향후 차량용 센서 시스템 IC에서의 자가진단을 통한 고신뢰성기술은 센서 검지부를 비롯하여 네트워크 및 신호처리에까지 확대될 것으로 예측된다.[2]
응용 분야 [ 편집 ]
자동차에 탑재된 센서
엔진 및 변속기 [ 편집 ]
압력센서 [ 편집 ]
압력센서는 기체나 액체의 기본적인 물리량의 하나인 압력을 감지하여 전기신호로 변환시킬 목적으로 사용되는 센서이다. 압력센서는 가전제품을 비롯하여 자동차, 생체공학용 의료기, 환경 제어와 산업체의 대규모 시스템제어 등에 광범위하게 응용되고 있다. 특히 차량용 압력센서는 파워트레인 제어, 주행안전 제어, 차체 제어 등 엔진 주변 중심으로 구동계 등에 확장 적용되고 있는 추세이며, 연비 향상, 배기가스 클린화, 안정성 향상 목적으로 적용 수량 및 활용도가 급격히 증가되고 있는 핵심 전장 부품이다. 압력센서는 최근 기계식에서 전자식으로 대부분 전환되었는데, 압력에 의해 변형되는 게이지부, 증폭부, 온도보상부 등으로 구성된다. 차량용 압력센서는 설계 및 제조 공정에서 온도, 진동, 외부의 충격, 전자기파 등의 기본 요구조건을 충족시켜야 한다. 압력센서는 적용 압력 범위에 따라 저압용, 중압용, 고압용으로 구분될 수 있으며, 중저압용으로 세라믹 압력센서와 실리콘형 압력센서가 적용되고 있고, 저가화, 대량 양산기술 진보에 따라 세라믹형 중압용 압력센서의 차량 적용이 급격히 증가되고 있다. 차량 연료송출압, 에어컨 냉매압력 측정 등 종래 필수적으로 적용되고 있는 압력 측정 시스템에서 온도 정보를 추가 수집하여 원 적용 시스템 제어 활용은 물론, ECU(Engine control unit)에서 이들 정보의 타 시스템 제어에 활용하기 위한 기술적 시도가 있어왔고, 온도센서를 복합화한 압력센서가 출시되고 있다. 압력, 온도 등 차량 모듈 제어에 핵심이 되는 이러한 정보의 ECU 활용을 위해서는 통신 기능이 추가된 신호처리용 집적회로(ASIC)의 사용이 필수적이며, 소형화를 통한 센서융합 등 제반 기술의 수평적 개발 및 활성화가 필요할 것이다. 자동차에 적용되는 압력센서는 반도체형으로 전화되었으며 대표적인 것으로는 압저항형 실리콘 센서(Piezo-resistive Pressure Sensor with Silicon senosr)와 정전 용량형 압력센서(Capacitive Ceramic Pressure Sensor)가 있다.[4]
압저항형 센서 (piezo-resistive pressure sensor with silicon senosr) : 실리콘 결정에 응력이 가해지면 저항값이 변화하는 피에조 저항효과의 원리를 이용한 센서이다. 이 센서의 특징은 높은 선형성과 주파수 범위의 영향을 받지 않는 히스테리시스(hysteresis) 등으로 고저밀도 측정에 적합하다.
(piezo-resistive pressure sensor with silicon senosr) : 실리콘 결정에 응력이 가해지면 저항값이 변화하는 피에조 저항효과의 원리를 이용한 센서이다. 이 센서의 특징은 높은 선형성과 주파수 범위의 영향을 받지 않는 히스테리시스(hysteresis) 등으로 고저밀도 측정에 적합하다. 정전 용량형 압력센서(capacitive ceramic pressure sensor) : 서로 마주보고 있는 전극판의 간격이 외부 응력에 의해 변화하게 되면 전극 간의 정전 용량 변화를 전기신호로 바꿔서 응력을 검출하는 원리를 이용한 방식이다. 압저항형에 비하여 온도 특성이 우수하고 고감도인 관계로 미세한 압력 측정에 주로 사용되나, 전극의 형성 및 외부회로와의 연결이 복잡한 구조로 되어 있어 응답성이 낮은 단점이 있다. MEMS에 의해 생산되는 압저항형 실리콘 센서는 자동차 엔진제어용으로 MAP 센서가 최초로 상품화되었으며 타이어 압력, 브레이크 압력, 오일 압력 및 에어컨 압력센서 등으로 확산 되고 있다.
MAP 센서(manifold absolute pressure) : 흡기 매니폴드 내의 압력 신호 및 엔진 회전수에 의해 공기량을 측정하고 연료와의 적정한 혼합비를 조절하기 위해서 사용되는 센서이다. 엔진 가까운 곳에 위치하기 때문에 고온(140~650℃)에 견딜 수 있도록 고온 특성이 좋은, 절연막 위에 형성한 반결정 실리콘을 기판으로 한 반도체인 SOI(silicon on insulator) 구조를 사용한다. 엔진실린더 내의 직접 장착되어서 연소되는 압력을 측정하는 연소압 센서(combustion pressure sensor)는 희박연소(lean burn) 엔진 개발과 더불어 실용화되기 시작했으며, 희박 연소제어로 연비향상, 배기가스의 정화를 할 수 있는 특징이 있다.
유량센서 [ 편집 ]
유량센서는 액체와 기체 등 유체의 흐름을 측정하는 센서이다. 유량은 압력, 온도, 레벨 등과 함께 산업현장에서 가장 많이 측정되는 측정량 중의 하나로, 가장 측정하기 까다로우며 그 방법도 정밀측정용, 공정용 등 측정 목적과 액체, 기체, 증기, 유체의 물성에 따라 매우 다양하다. 유량 측정은 다릉 측정량과는 달리 직접 유량을 측정하는 방식은 매우 적으며 다른 물리량을 측정하고 이 측정된 정보로부터 유량을 산출하는 방식이 대부분이다.[5] 자동차에서 엔진에 흡입되는 공기량은 스로틀 밸브의 열림량과 흡기관 내의 압력, 엔진 회전수에 따라 대략 결정되므로 각각의 값을 검출하기 위한 센서를 총칭해서 유량센서라고 한다. ECU에서는 이 유량센서에 의해 기본 연료 분사량을 연산한다.[6] 연료개질장치를 수반하는 고체고분자형 연료전지(PEFC)는 개질기와 연료전지 자체의 효율을 적정하게 평가하기 위해 장치에 투입되는 원 연료의 공급량을 계측할 필요가 있고, 개질 시에 생성되어 전지촉매의 성능에 악영향을 미치는 일산화탄소 농도를 낮추기 위한 공기유량 제어도 필요하다. 연료전지 시스템의 적절한 운전과 고효율 측면에서 가스나 공기의 유량계측은 매우 중요하며, 보급을 위해 소형화와 낮은 비용, 양산성이 우수한 유량센서가 요구되어 왔다. 그러나 실제로는 주변온도의 변화와 배관방식에 의한 유입조건, 맥동발생 등에 따라 적용이 쉽지 않았다. 이에 따라 이러한 과제를 해결하고, 모든 환경에서 정밀한 유량계측을 할 수 있는 센서 디바이스를 이용한 MEMS 유랑센서가 개발되었다. 연료전지 시스템의 유량계측은 연료가스 유입원, 배관방법, 온도변화와 같은 여러 요인이 계측 시에 영향을 미친다. MEMS 유량센서에서는 이러한 영향을 줄이기 위한 대책을 강구하고 있다. 유량센서의 출력은 히터의 상류측과 하류측 사이의 온도차에 의존하기 때문에 양호한 온도 특성을 얻기 위해서는 히터온도를 주변온도보다 일정한 수준으로 높게 유지하고 히터 상·하류의 온도차가 주변온도에 의존하지 않도록 해야 한다. MEMS 유량센서는 센서 디바이스 부근의 난류나 불균일한 유속분포를 해소하기 위해 최적의 유로를 설계하며, 상류배관을 어떤 방향에서 접속해도 같은 유량의 출력변동을 받는다. 따라서 MEMS 유량센서는 유입부에 직관 배관만을 설치하지 않고 연료전지 시스템의 배관설계 자유도를 높여 공간절약을 실현할 수 있다. 연료전지 시스템에 사용되는 블로어(blower)와 같은 공급원에 따라서는 발생유량이 주기적으로 변하는 맥동현상이 나타난다. 이런 맥동환경에서는 정확한 유량계측이 곤란하므로 일부 MEMS 유량센서에서는 센서 디바이스 하류측에 오리피스를 설치하여 맥동영향에 의한 출력 불안정 현상을 제어하는 구조를 채용하고 있다.[7]
가속도센서 [ 편집 ]
가속도센서는 물체에 작용하는 가속, 진동 및 충격 등의 동적 힘을 순간적으로 감지하는 센서이다. 따라서 자동차, 기차, 항공기 및 선박 등 운송기기와 공장자동화 관련 장비 등에 폭 넓게 활용할 수 있다. 특히, 최근에 자동차의 안정도에 관한 관심이 높아지면서 정면충돌시 운전자와 승객을 보호하기 위한 안전장치로 에어백의 설치를 법규화 하면서 에어백에 들어가는 핵심 소자인 차량용 가속도센서에 대한 연구가 많이 이루어지고 있다. 또한 자동차의 안정성, 신뢰성, 안락성, 편의성 향상을 위하여 가속도센서는 전자식 엔진제어장치(ECU), 잠김방지제동장치(ABS), 지능형 현가장치, 스티어링 시스템 등의 핵심부품으로 사용되고 있다. 기계식 가속도센서는 구조가 복잡하고 크고 무거우며 양산이 힘들어 신뢰성이 낮고 가격이 높아 그 활용이 제한된다. 반면에 실리콘 가속도센서는 실리콘의 기계적 성질이 우수하고 기존에 확립된 반도체 집적회로 공정기술을 이용함으로써 신뢰성과 양산성이 우수하며, 소자의 소형화, 경량화 및 저가격화가 가능하다는 장점이 있다. 실리콘 가속도센서는 박막형성이 용이한 다결정 실리콘을 표면 마이크로머시닝하여 만든 용량형과 단결정 실리콘 위에 압저항 소자를 제작하고 이를 마이크로머시닝으로 박막 가공하여 만든 압저항형으로 분류할 수 있다.[8] 실리콘 가속도센서는 크게 3가지 부분으로 나누어진다. 가속도 즉, 힘을 받아들이는 실리콘 미세기계 구조부와 힘을 전기적 신호로 바꾸어 주는 변환소자부, 정격출력을 만들어 주는 신호처리부로 구성된다. 미세기계구조물 제작을 위한 마이크로머시닝기술은 집적회로 제조기술을 기반으로 하고 있으나, 공정자체가 반드시 일치하는 것은 아니다. 특히, 영점, 감도, 온도보상 및 자기진단회로가 센서부와 같이 단일 칩에 집적화되는 온칩(On-chip) 센서의 개발추세에 따라 기존의 공정기술과 마이크로머시닝기술의 호환성, 재현성 및 안정성을 유지하는 상호보완적인 공정기술이 강조되고 있다. 양산을 위한 가장 중요한 기술은 실리콘 미세구조를 만드는 미세가공기술이며, 웨이퍼 단위에서 얼마나 균일하고 재현성 있는 실리콘 구조물을 제작할 수 있느냐 하는 것이 기술의 관건이라 할 수 있다. 변환소자부는 감지원리에 따라 압전형, 압저항형, 용량형 등으로 나눌 수 있다. 압전형은 산화아연(ZnO)과 같은 압전물질의 응력에 대한 전기분극을 이용하며, 직류(DC) 가속도의 측정이 불가능한 단점이 있다. 압저항형은 확산에 의한 저항만 형성하면 되므로 다른 센서에 비하여 공정이 간단하며, 선형성 및 주파수 특성이 좋으며 직류가속도의 측정이 가능하다. 정전용량형은 미세구조부의 변위에 의한 정전용량변화를 측정하며, 감도가 높은 반면에 공정이 상대적으로 복잡하다. 주파수 변환 회로가 하나의 칩 내에 실장 되어야 하며, 선형성이 나쁜 단점이 있다. 그중 압저항형 가속도센서는 압전형과 용량형의 중간적인 특성을 나타내고 있으며, 구조 및 신호처리가 단순하고 요구되는 성능을 만족시키면서 저렴한 가격으로 제조할 수 있는 장점이 있다.[9]
온도센서 [ 편집 ]
온도센서는 온도를 측정하는 센서이다. 자동차 온도센서는 ‘서미스터(thermistor)’라고 하는 전자장치가 주로 사용된다. 이는 온도에 따라 전기 저항이 변하는 반도체의 성질을 이용한 소자이다. 그중에서도 NTC(negative temperature coefficient)라고 하는 서미스터가 사용된다. 이러한 저항값을 측정한 데이터를 다시 온도 정보로 변환해 자동차 실내에 표시하는 방식이다. 자동차 실외 온도 측정은 자동차 상황에 따라 끊임없이 변화한다. 아무리 제어를 한다고 해도 장시간 고속도로를 달리고 있다면 실제 외부 온도보다 내려가고, 지열이 올라오는 아스팔트 주차장에 장시간 주차하면 온도는 오르기 마련이다. 전문가들은 실제 기온과 비교해 플러스 마이너스 3도 정도의 오차가 발생할 수 있다고 하지만 그 이상 온도가 차이가 자주 발생 한다면 센서 불량의 가능성도 있기 때문에 점검을 받아보는 것도 좋다. 차종 마다 조금씩 다르겠지만 대부분 자동차 외부 온도센서는 앞 범퍼 개구부나 번호판이 부착된 범퍼 안쪽에 숨어있다. 높이는 지상에서 약 30cm 정도에 설치된다. 이렇듯 비교적 엔진룸과 가까운 위치이기 때문에 엔진에서 발생하는 열로 인한 영향을 받는다. 하지만 주행 중에 외기로 인한 냉각도 동시에 이뤄지기 때문에 적당히 상쇄되며, 만약 공회전 중이라고 해도 크게 변동되지 않도록 전자식으로 제어되고 있기 때문에 최대한 외부 온도와 비슷하게 측정된다. 특히 지면에서 적당히 떨어져서 설치되어 있는 것도 중요한데, 아스팔트와 같이 지면에서 올라오는 뜨거운 열로 인해 오차가 발생될 수 있지만 약 30cm 정도 떨어진 상태에서 주행으로 발생하는 바람을 맞게 되면 대부분은 상쇄된다. 그럼에도 불구하고 오차가 아주 없는 것은 아니다. 측정할 당시 자동차의 위치나 주변 환경에 따라 외부 공기 온도와는 약간의 차이를 보일 수 있다. 가장 정확한 측정 상태는 시동을 걸어 출발 후 적당한 거리를 주행했을 때이며, 이러한 상황을 상정해서 온도센서가 설정되어 있기 때문이다.[10]
자이로센서 [ 편집 ]
자이로센서는 가로, 세로, 높이의 3개 축을 기준으로 움직임을 인식하는 센서이다. 자이로스코프는 회전에 의해 발생하는 다량의 회전운동 에너지를 보유하게 될 때, 각 운동량 보존 법칙에 따라 회전축 방향이 잘 변하지 않기 때문에 회전축 방향으로 정렬을 유지한다. 고속으로 돌아가는 자이로의 회전축은 그 방향이 쉽게 변하지 않는다는 것을 이용하여, 원점 위치를 역으로 추정하여, 현재의 방향이 어느 쪽인지를 역산출하는 기계다. 그래서 방향성을 측정할 때 쓰게 된다. 비슷한 센서로는 지표면을 기준으로 기울기를 측정하는 가속도센서가 있다. 자이로스코프를 가장 쉽게 표현한다면 ‘팽이’라고 할 수 있다. 회전 중인 팽이는 외력이 0인 상태에서 회전력에 대한 관성을 가진다. 팽이가 돌고 있는 지표면에 각도가 생겨도 팽이의 중심축은 지구 중심 방향을 향하는 현상을 보면 알 수 있다. 고속 회전하는 회전자에 외력이 없다면 로터의 각 운동량 벡터값은 항상 일정하다는 것이 방향 안정이다. 회전축을 중심으로 균형을 유지하며 방향이 바뀜에도 회전자는 회전축을 중심으로 밸런스를 유지한다. 외부 틀은 함께 회전하며 기준 좌표계로부터 틀어진 정도를 측정한다. 로터가 외부로부터 로터의 축 방향으로 힘을 받으면 회전 반발력이 생겨 로터에 수직한 또 다른 수직축 방향에 대한 회전운동을 시작한다. 회전운동은 회전축을 중심으로 이루어진다. 외력을 가하거나 시간이 지나 스스로 멈추려 할 때, 축을 중심으로 회전운동을 방해하는 외력이 크다면 멈출 것이고 작다면 다시 중심을 잡고 회전할 것이다. 이러한 현상을 세차운동이라 정의한다. 광학식 자이로센서는 빛의 간섭효과 등을 이용하여 만든 자이로스코프이다. 개념 자체는 굉장히 오래되었으나 1960년대 후반부터 항공기나 미사일 등의 정밀 센서로 각광을 받고 있다. 일반적인 반도체 자이로스코프에 비해 극도로 높은 정밀도를 가지기에 비행기나 탄도미사일 등 관성항법을 수행하는 경우엔 꼭 이 광학식 자이로를 사용한다. MEMS 자이로센서는 초소형의 자이로스코프이며 보통 일반 반도체 칩 정도의 크기이다. 코리올리(coriolis) 효과의 힘을 이용한 튜닝포크 방식의 센서로서, 대부분의 모바일기기에 이 센서가 채용되었다. 코리올리 힘을 측정하여 전기 신호로 변환하고 힘에 대한 각속도를 계산한다. 튜닝포크 방식이란 무한 진동하는 추 2개를 이용해 모든 방향에서 작용되는 회전력을 측정할 수 있도록 하는 방식이다.
조향각센서 [ 편집 ]
조향각센서는 자동차 조향장치에서 사용되는 센서이다. 운전자가 조작하는 핸들의 회전 각도,방향,속도 등을 감지해 관련 정보를 자동차 전체의 움직임을 제어하는 VDC(vehicle dynamic control) 시스템에 전달하는 역할을 한다. VDC시스템은 센서가 보내는 정보로 자동차 서스펜션이나 ABS브레이크 등의 안전주행장치를 제어한다. 조향각센서는 미래형 자동차에 도입될 무인운전 시스템, 자동주차, 차선이탈 경보 시스템 등 최첨단 장치의 중추적인 역할을 한다. 특히 향후 운전자 편의성을 대폭 향상시키기 위해 기존의 기계식 조향장치가 전동식으로 바뀌면서 그 중요성이 더욱 커지고 있다.[11]
친환경 [ 편집 ]
배기가스센서 [ 편집 ]
배출가스 정화 시스템에서 사용되는 배기가스센서는 배기가스를 감지하여 ECU에 전달하는 센서이다. 배기가스 중에 함유된 산소의 양을 측정하여 출력전압을 ECU로 전달하고 연료 분사시간을 제어하여 항상 이론 공연비인 14.7:1에 가깝도록 조정한다. 일반적으로 차량용 센서는 섭씨 영하 40도에서 120도의 범위에서 사용되는데, 배기가스 센서의 경우에는 600도에서 800도의 고온에서도 견딜 수 있는 내구성을 갖춰야한다.[12] 온도의 급격한 변화, 중력의 30배가 넘는 가속과 충격, 각종 화학물질과 수분, 유류 등으로 인한 오염과 부식에 대비해야 할 뿐 아니라, 지속적인 진동과 충격에도 정상적인 동작을 유지해야 한다. 또한 외부와의 통신 측면에 있어서도 최대 100㎞/h가 넘는 고속에서도 안정적인 연결이 유지되야 한다.[13]
산소센서 [ 편집 ]
산소센서는 가솔린 엔진의 연료 분사장치와 배출가스 유해물질 제어를 가능하게 한다. 공기와 연료의 비율을 적합하게 제어하는데 핵심적인 역할을 하기 때문에 산소센서에 이상이 발생하면 엔진제어장치(ECU)는 정확한 공연비를 감지할 수 없게 되고, 결국 추정치에 의존하게 된다. 공연비에 대한 정확한 감지가 불가능해지면 차량의 성능이 감소하고, 배출가스 같은 유해물질의 증가를 초래한다. 가솔린차에는 보통 두 개의 산소센서가 장착되어 있다. 촉매 장치의 전단에 위치한 전방 산소센서와 후단에 위치한 후방 산소센서로 나뉘어진다. 전방 산소센서는 정밀한 연료량의 제어를 위한 데이터를 ECU에 제공하고, 후방 산소센서는 부가적인 제어 및 촉매장치의 성능을 모니터링하기 위한 데이터를 ECU에 제공한다. 엔진의 작동 싸이클 중에서 배기행정(exhaust stroke) 단계에서는 고온 고압의 배기가스가 배기밸브를 통해 실린더 외부로 배출되는데, 이 가스는 배기 매니폴드와 전방 산소센서를 지나서 촉매 장치로 들어간다. 지르코니아 센싱 소자는 산소센서 내부에 위치해 있으며 금속 소재의 하우징에 싸여있다. 배기가스에 포함되어 있는 산소 분자는 센서의 금속쉘에 뚫린 미세한 구멍을 통해 센싱 소자에 도달한다. 이 센싱 소자의 반대편에는 신선한 공기가 모여 있는 에어챔버가 있는데, 배기가스와 에어챔버 간의 산소 분압 차이에 의해 산소 이온이 센싱 소자를 거쳐 이동할 때 기전력이 발생하게 된다. 대기 중 산소 농도는 일정하므로, 이때 유도되는 기전력의 크기는 배기가스 중의 산소 농도에 의해 결정된다.[14] 이처럼 산소센서가 보내는 신호를 기준으로 ECU는 최적화된 공연비의 제어상태를 유지한다. 일반적으로 가솔린 엔진에서 탄화수소와 일산화탄소는 냉간 시동 후 30초 이내에 대부분의 양이 배출된다. 때문에 빠르게 활성화되는 산소센서는 배출가스 저감에 중요한 역할을 한다. 산소센서의 빠른 활성화 속도는 두 가지 기술을 통해 구현된다. 센싱 소자의 질량을 줄이고 히터에 가해지는 파워를 증가시키는 것이 그것이다. 센싱 소자의 질량 감소는 세라믹 소자의 모양을 원뿔에서 평판형으로 전환함으로써 해결된다. 히터의 파워 증가는 히터의 탑재방식을 변경시킴으로써 이루어진다. 원뿔형 소자는 분리된 히터를 사용하는 반면 평판형 소자는 센서 레이어 내부에 집적된 히터를 사용한다. 기존의 방식 대비, 약 50% 가벼워진 평판형 소자를 이용함으로써 작동 최적온도에 도달하는 시간은 10초 이내로 단축된다.[15]
편의성 [ 편집 ]
일사센서 [ 편집 ]
일사센서는 차량 주변의 빛을 감지하는 센서이다. 조도센서라고도 한다. 빛의 세기에 따라 전기적 성질이 변화하는 광다이오드의 원리를 이용하고 있는 것이 특징이다. 광다이오드는 광센서의 일종으로 빛의 양에 따라 저항값이 변화하는 특성을 가지고 있다. 일사센서는 이러한 저항값의 변화를 전류 또는 전압으로 변환해 오토라이트 컨트롤러가 차량 주변의 광원이 밤인지 낮인지 또는 터널이나 지하주차장인지를 판단하는 기준을 제공한다. 초기의 오토라이트 컨트롤 시스템은 윈드실드 하단의 센터페시아 정중앙에 있는 일사센서를 이용해 시스템을 제어하는 방식을 주로 사용해 왔다. 이러한 이유는 오토라이트 컨트롤 시스템이 적용되기 이전부터 일사센서가 전자동에어컨(FATC)의 중요한 입력센서 중 하나로 사용되어 왔기 때문이다. 일사센서는 전자동에어컨시스템에서 자동차 실내로 들어오는 빛의 양에 따라 실내온도 변화를 감지해 전자동에어컨 컨트롤러가 운전자가 설정한 온도에 따라 에어컨의 토출온도와 풍량을 제어할 수 있도록 도와주는 역할을 한다. 빛의 세기에 따라 광원의 밝기와 온도변화를 감지하는 것만 다를 뿐 작동원리는 같다. 최근에는 이러한 일사센서에 오토라이트 기능과 도난방지시스템 작동램프나 우적감지 기능 등 다양한 기능을 통합해 사용되고 있는 추세다. 우적감지 와이퍼 시스템의 적용된 경우에는 일사센서가 윈드실드 상단에 위치한 우적 감지센서와 일사센서 등과 통합되어 있는 방식이 주로 사용되고 있으며, 일사센서보다는 다기능을 갖추고 있다보니 콤비 센서라고도 불린다. 우적감지 와이퍼와 통합되어 윈드실드 상단에 위치한 일사센서의 경우 센터페시아 상단에 위치한 일사센서 방식보다 직접적으로 빛을 감지하므로 직관적이고 감도가 민감할 뿐 아니라 외관상으로도 유리한 측면이 많다. 반면 센터페시아에 일사센서가 위치한 경우에는 전면유리를 통해 빛의 양을 감지하므로 유리의 반사율이나 주변환경에 따라 차이를 보이기도 한다. 예를 들면 전면유리에 가시광선 투과율이 낮은 틴팅 처리를 한 경우 어두운 그늘만 드리워도 오토라이트가 작동하는 현상이 대표적이라 할 수 있다. 한편 같은 오토라이트 시스템이라도 터널을 지날 때 자동차 제작사나 차종마다 오토라이트가 작동하는 시간이 다르다. 어떤 차는 터널에 들어서자마자 라이트가 켜지지만 또 다른 차종은 한참 지나서 라이트가 켜진다. 터널을 빠져나와서도 라이트가 꺼지는 시간이 상이하다. 해질 무렵과 같은 어중간한 밝기에서도 마찬가지인데, 그 이유는 자동차 회사마다 또는 차종마다 정해진 작동기준, 즉 일사센서의 작동전압 기준이 다르기 때문이다.[16]
우적센서 [ 편집 ]
우적센서는 자동으로 와이퍼를 작동시키는 센서이다. 레인센서라고도 한다. 초창기 와이퍼 스위치는 내리는 빗물 변화에 따라 운전자가 직접 와이퍼 속도 조절 레버를 움직여야 했지만 우적센서는 운전자가 와이퍼 속도 조절 스위치를 조작할 필요가 없다. 우적센서는 비의 양이 많아지면 와이퍼의 작동 속도가 빨라지고, 비의 양이 적어지면 느려지다가 비가 멈추면 작동을 멈추기까지 자동으로 작동한다. 우적센서는 발광다이오드와 광다이오드가 같이 들어있는 구조이다. LED등과 같은 원리로 반도체의 에너지 간격이 작아서 적외선 부분의 빛을 내는 발광다이오드가 달려있고 옆에는 빛을 받으면 전류로 만드는 광다이오드가 있다.[17] 원리는 자동차 앞 유리창 상단 중앙에 달린 센서가 적외선을 발사한 뒤 이 적외선이 부딪쳐 다시 센서로 돌아오는 사이의 파장을 감지하는 것이다. 유리창 바깥에 빗물이 고여 있을 경우 난반사가 일어나 센서가 이를 감지하고 와이퍼를 작동하게 되는데 이때 센서는 빗물의 양까지 알아서 판단해 와이퍼의 속도까지 자동으로 조절해 준다. 우적센서는 직경 0.4mm의 아주 작은 빗방울도 감지할 수 있으며 투과율을 스스로 보정하도록 되어 있어 코팅 등으로 유리의 투과율이 불량하더라도 알아서 감지할 수 있다. [18]
실내환경 [ 편집 ]
습도센서 [ 편집 ]
습도센서는 대기 중의 수증기로 인하여 유기 고분자나 세라믹의 저항 값 유전율 등이 변화하는 성질을 이용하여 습도를 전기적으로 검출하는 센서이다. 두 개의 전극 상에 도전 성분과 고분자로 만들어진 막이 겹쳐지면, 습도가 높을 때는 고분자가 팽창함에 따라 도전 성분 간의 간극이 넓어져 전극 간의 전기 저항이 증가한다.[19] 고급차의 전자동 환기 조정 장치에는 습도센서가 대부분 탑재되어 있는데, 실내 습도가 높아지면 온도에 관계 없이 에어컨이 가동되는 것 또한 습도센서의 역할이다.[20] 리어윈도의 흐림 방지 제어 등에도 이용되고 있다.
가스센서 [ 편집 ]
가스센서는 자동차 등에서 배출하는 가스를 측정하는 센서이다. 차량의 대수가 늘어남에 따라 차량에 의한 대기오염 문제 또한 주요한 문제로 대두되고 있다. 차량은 다양한 배기가스를 배출하고 있으며, 이 중에서 특히 이산화탄소와 이산화질소는 인체에 매우 유해한 가스로 알려져 있다. 이 때문에, 이러한 유독가스인 이산화탄소와 이산화질소를 차량에서 바로 감지하고 이를 제어하려는 요구가 급속히 높아지고 있다. 이를 위해서는, 차량의 가스를 직접 감지하기 위한 가스센서의 개발이 필수적이다. 일반적으로 가스센서는 반도체식, 고체전해질식, 접촉연소식 등이 사용되고 있으며, 이 중에서 반도체식은 센서 제작이 용이하고, 다양한 범위의 가스검출이가능하여 많이 연구되고 있는 센서이다.[21]
녹스센서 : 질소산화물이 대기로 배출되지 않도록 감지하는 센서이다. 전단 녹스센서, 후단 녹스센서는 차량에서 배출되는 질소산화물량을 측정하여 ECU에 전달하는 역할을 하는 차량의 부품이다. 질소산화물은 질소와 산소의 화합물로, 연소 과정에서 공기 중의 질소가 고온에서 산화되면서 발생한다. 대표적으로 자동차, 항공기, 선박, 산업용 보일러, 소각로, 전기로 등이 질소산화물의 배출원으로 꼽힌다. 질소산화물은 일곱 종류가 알려져 있는데 공해 문제에서 중요한 것은 일산화질소와 이산화질소이다. 질소산화물은 교통량과 일광에 따라 크게 영향을 받는다. 기관지염증과 천식, 만성기관지염을 일으키며 자각 증상으로는 기침, 가래, 눈물, 호흡곤란 등이 나타난다. 특히 급성 중독 시에는 폐수종을 일으켜 사망에 이르게 하는 무서운 물질이다. 아울러 질소산화물은 산성비의 원인이 될 뿐만 아니라 식물을 고사시키는 등 주요 대기오염물질로 규제되고 있다. 특히 질소산화물이 태양광선과 반응하면 오존이 생성되는데, 대기 중 오존의 농도가 높아지면 호흡기와 눈에 자극이 심해지고 기침을 유발한다.[22] 디젤엔진에서 배출되는 배기가스가 DPF를 지나 배출되는 질소산화물량을 녹스센서가 측정하여 차량 컴퓨터인 ECU에 프로그램된 요소수 분사량을 결정하게 된다. 요소수 노즐에서 분사된 요소수는 차량 온도에 수분은 증발하고 요소수 분자가 질소산화물을 포집하여 SCR촉매를 지난 후 후단 녹스센서에서 차량에서 배출되는 질소산화물량을 다시 한 번 측정한다.[23]
AQS [ 편집 ]
AQS(air quality sensor)는 공기오염도가 높은 지역을 지나갈 때 운전자가 별도의 스위치 조작을 하지 않더라도 외부 공기 유입을 자동으로 차단하는 센서이다. 대한민국에는 유해가스 차단장치로 알려져 있으며, 5cm*7cm 크기의 센서가 라디에이터 앞이나 범퍼 뒤에 부착되어 악취, 질소산화물, 산화성 가스, 일산화탄소 등 매연을 차단한다. 이렇게 유해물질을 차단하여 차량 내부를 쾌적한 상태로 유지시키고 운전자가 운전에 집중할 수 있도록 돕는다. AQS는 100퍼센트 차단하는 기능이 아니기 때문에 적게나마 유해물질이 차량 내부로 들어올 수 있으며 외부 공기가 완전히 차단되기 때문에 특정 계절에 윈드실드가 뿌옇게 되어 시야를 방해하는 경우가 생길 수 있다. 또한 센서가 비교적 반응이 느려 기능이 작동될 때까지 잠시 동안 유해물질이 유입될 수 있다. 한편 AQS는 2000년대 초반에는 자주 보이다가 이후 출시되는 대부분의 차량에는 탑재되지 않고 있다. 반응이 느리고 하수구 냄새 등 악취에 대해서 차단을 잘 하지 못하는 경우가 많아 차량 내부순환 버튼을 주로 많이 사용하기 때문이다.[24]
충돌방지센서 [ 편집 ]
충돌방지센서는 자동차 전방 장애물에 대하여 충돌을 피하거나 충돌 위험을 줄이기 위해 탑재되는 센서이다. 전방의 상황을 영상으로 감지하는 카메라, 전방·후방·측면의 물체를 확인하는 레이더가 대표적이다. 이외에도 시스템이 작동하는 데는 자동차 속도를 감지하는 휠 속도센서, 스티어링의 움직임을 감지하는 조향각센서, 차량의 수직측 회전을 감지하는 요레이트센서, 엔진 컨트롤러, 브레이크 제동 컨트롤러 등의 많은 센서와 컨트롤러 등이 유기적인 통신을 이용한 정보를 통하여 차량충돌 위험 단계에 따라 경고문 표시, 경고음 발생으로 충돌위험성을 단계별로 운전자에게 경고한다. 이와 동시에 브레이크를 제어하여 탑승자를 보호하며 주행안전을 보조한다. 전방 충돌방지 보조시스템 작동은 자동차 시동 후 전방충돌방지 보조, 또는 충돌 경고로 설정하고 각각의 감지센서가 정상적으로 작동할 수 있는 상태이어야 한다. 각각의 센서가 정상적이지 않을 경우 시스템이 작동이 되지 않는다는 경고사인을 클러스터에 표출한다. 시스템에 이상이 없는 상태에서 전방에 조건을 만족할 경우 시스템은 작동 상태가 된다. 주요 충돌방지센서는 다음과 같다.
전방 카메라 : 전방의 차량과 보행자, 자전거탑승자 등을 촬영하여 감지하는 기능을 한다. 장착위치는 실내안쪽에 룸미러 뒤쪽 앞 유리창 중앙 상단에 장착되어 있다. 다른 센서들과 통신을 통하여 촬영정보를 주고받게 되어 있으며 작은 카메라이자 컴퓨터모듈이다. 주의할 점은 전방유리에 이물질로 오염이 심하거나 눈, 비 등이 카메라 시야를 방해할 경우에는 정상적인 감지 작동이 어렵기 때문에 청결한 관리가 필요하다.
: 전방의 차량과 보행자, 자전거탑승자 등을 촬영하여 감지하는 기능을 한다. 장착위치는 실내안쪽에 룸미러 뒤쪽 앞 유리창 중앙 상단에 장착되어 있다. 다른 센서들과 통신을 통하여 촬영정보를 주고받게 되어 있으며 작은 카메라이자 컴퓨터모듈이다. 주의할 점은 전방유리에 이물질로 오염이 심하거나 눈, 비 등이 카메라 시야를 방해할 경우에는 정상적인 감지 작동이 어렵기 때문에 청결한 관리가 필요하다. 전방 레이더 : 모듈 내부에 레이더 전자기파를 이용하여 물체에 부딪쳐서 반사하는 신호를 해석, 전방 장애물과 거리, 속도를 측정한다. 전방 차량유무 속도 거리에 따라 최적의 가감 속도를 계산한다. 이후 가감속된 정보를 브레이크 컨트롤러로 전송한다.
: 모듈 내부에 레이더 전자기파를 이용하여 물체에 부딪쳐서 반사하는 신호를 해석, 전방 장애물과 거리, 속도를 측정한다. 전방 차량유무 속도 거리에 따라 최적의 가감 속도를 계산한다. 이후 가감속된 정보를 브레이크 컨트롤러로 전송한다. 전측방 레이더 : 전방 범퍼 내측 좌우에 장착되어 있으며 레이더는 전자기파를 이용하여 전측방 좌우 차량의 유무를 감지하여 거리 및 속도를 측정한다, 레이더 전자기파는 대부분 24 기가헤르츠(GHz) 대역의 레이더를 사용하고 있다. 특히 시야 확보가 쉽지 않은 야간 혹은 우천 환경에서 차선을 변경할 경우, 위험경고 문구 및 경고음을 운전자에게 인식하도록 제공하여 안전하게 운전할 수 있도록 편의를 제공한다. 전측방레이더는 전방에 교차충돌을 예방하며 크루즈 컨트롤 기능과 고속도로 주행을 보조하는 기능도 있다.
: 전방 범퍼 내측 좌우에 장착되어 있으며 레이더는 전자기파를 이용하여 전측방 좌우 차량의 유무를 감지하여 거리 및 속도를 측정한다, 레이더 전자기파는 대부분 24 기가헤르츠(GHz) 대역의 레이더를 사용하고 있다. 특히 시야 확보가 쉽지 않은 야간 혹은 우천 환경에서 차선을 변경할 경우, 위험경고 문구 및 경고음을 운전자에게 인식하도록 제공하여 안전하게 운전할 수 있도록 편의를 제공한다. 전측방레이더는 전방에 교차충돌을 예방하며 크루즈 컨트롤 기능과 고속도로 주행을 보조하는 기능도 있다. 후측방 레이더 : 후측방 범퍼 내측 좌우에 장착되어 있으며 후측방 차량의 유무를 감지하여 거리 및 속도를 측정한다, 레이더 전자기파는 대부분 24 기가헤르츠 대역의 레이더를 사용하고 있다. 특히 시야 확보가 쉽지 않은 야간 혹은 우천 환경에서 차선을 변경할 경우, 위험을 알려주어 운전자가 더욱 안전하게 운전할 수 있도록 편의를 제공한다.[25]
이미지센서 [ 편집 ]
이미지센서는 카메라 렌즈로 들어온 영상정보인 빛을 디지털 신호로 바꾸는 센서이다.[26] 이미지 센서는 스마트폰 카메라, 디지털카메라, CCTV뿐만 아니라, 자율주행 자동차에도 필수적이다. 스마트 이미지 센서에는 빛을 전기 신호로 전환하는 부분과, 잡음이나 간섭과 같은 현상을 제거하며 데이터를 압축하기 위한 프로세서(ISP)와 메모리가 들어간다. 자율주행 자동차 시장이 성장하며 휴대전화 뒷면처럼 자동차 내외부가 이미지 센서로 도배되고 있다. 기본적으로 이는 안전 주행을 위한 차량 및 차선 인식에 사용되는데, 사람과 교통신호, 도로 표지판 인식에도 필요하다. 영상 인식을 통해서 주행 중 다양한 물체를 파악하고, 보행자를 탐지하며, 대상과의 거리와 공간 정보를 인식한다. 그리고 도난 방지, 운전자의 졸음, 감정과 건강 상태 관찰에도 사용된다. 하지만 이러한 이미지센서가 자동차에 실제 사용되기 위해서는 일반 상용 반도체에 비해서 매우 엄격한 테스트와 패키징 과정을 거쳐야 한다. 자동차는 북극에서도 정상 동작해야 하고, 적도 사막에서도 안전하게 운행되어야 하기 때문이다. 특히 엔진 근처는 온도가 매우 높다. 그래서 보장되어야 하는 테스트 조건이 휴대폰이나 가전 기기에 들어가는 반도체보다 휠씬 가혹하다. 이미지센서는 메모리 반도체와 구조적으로 그리고 공정상에서 매우 유사한 점이 많다. 메모리는 격자 모양으로 규칙적으로 기억 셀을 설치한다. 마찬가지로 이미지 센서에도 화소들이 평면에 격자 구조로 배열된다. 그 화소의 크기도 나노 단위로 계속 줄어들고 있다. 초격차 메모리에서 확보한 나노 공정 기술과 설계 기술이 그대로 이미지센서에 적용된다. 거기에 인공지능(AI)과 패키징 기술이 결합하면 국제적으로 최고 경쟁력을 확보한다. 이미지센서가 바로 시스템 반도체 산업의 성장과 자동차 반도체 확보 경쟁에 전략적 돌파구로 여겨지는 까닭이다.[27]
에어백센서 [ 편집 ]
에어백센서는 충돌의 강도를 측정하는 센서이다. 이 센서가 측정한 충격량에 따라 에어백 팽창 여부를 결정하고, 만약 에어백을 전개해야 한다고 판단하면 인플레이터에 신호를 보낸다. 인플레이터는 내부의 화학 물질을 반응시켜 기체를 생성하고, 기체는 숨어있던 에어백을 순식간에 부풀린다. 참고로 이 모든 과정은 불과 0.03~0.05초 이내에 진행된다. 탑승자가 운전대나 대시보드에 부딪히지 않게 보호해야 하기 때문이다.[28]
TPMS [ 편집 ]
TPMS는 차량용 공기압 감지장치(Tire Pressure Monitoring System)의 약자로, 차량이 주행 중일 경우 타이어 내부의 압력과 온도를 측정하는 센서이다. TPMS가 세계 최초로 적용된 차는 1980년대 등장한 포르쉐(Porche) 959가 처음이지만, 보다 적극적으로 TPMS 개발의 동기가 된 것은 지난 1990년대 포드(Ford)의 익스플로러에 장착된 타이어 파손에 따른 사고로 인해 포드와 파이어스톤 사이에서 치열한 공방전이 일어나면서부터라고 할 수 있다. 이전까지는 공기압에 대한 중요성을 인지하면서도 적절한 대안을 찾지 못했던 자동차 업계와 소비자들은 이 사건을 계기로 TPMS를 통해 사람과 차의 안전성을 높이고 차의 성능과 타이어의 수명까지 연장시킬 수 있는 방안을 마련하게 되었다. 타이어 공기압 감지 장치는 차량의 타이어 내부에 직접 삽입되어 주행중 차량의 공기압 상태 및 온도 변화를 감지해 사용자에게 시청각적으로 알려준다. 타이어 내부에 삽입되는 TPMS 센서모듈은 특히 영하 40도에서 영상 180도의 가혹한 운행조건에서 최소 10년을 견뎌야 하기 때문에 일반차량용 전자기술과는 차원이 다른 기술이 필요하다.[29] 2007년 미국을 시작으로, 유럽연합(EU)도 2012년부터 TPMS 장착이 의무사항이 되었으며, 대한민국의 경우에는 2013년부터 판매되는 새로운 자동차에 한하여 TPMS가 의무 적용되기 시작하였다. TPMS은 공기압이 일정수준 이하로 낮아지면 경고신호를 발생시키고, 더 낮아져 위험한 상황이 되면 경보를 발생하여 운전자가 자동차를 정차시킬 수 있도록 하게 되는 데 작동방식에는 직접방식과 간접방식이 있다. 간접방식의 경우 특정 타이어의 공기압이 부족하게 되면 타이어의 둘레가 작아지게 되어, 도로주행 중 해당 타이어 바퀴의 회전속도가 빨라지게 되는 데, 이러한 원리를 특정 타이어의 공기압 이상 으로 판단하는 것이다. 즉 간접방식 TPMS에서는 ABS장치에서 바퀴 회전속도를 감지하는 용도로 사용되는 4개의 휠스피드센서(wheel speed sensor)의 신호를 받아 그 변화를 논리적으로 계산하여 타이어의 내부 공기압력 상태를 간접적으로 유추하는 방법을 사용한다. TPMS의 초기 적용단계에서는 사용되었으나, 타이어 마모에 의한 영향도와 오프로드와 같은 비포장도로 주행 시 신뢰도가 떨어지는 단점이 있어 현재는 거의 사용되지 않고 있다. 직접방식 TPMS는, 타이어의 공기 주입 밸브에 각각 타이어 압력센서가 부착되고, 이 압력센서들로 부터 타이어 압력과 온도를 감지하여 직접 계측하고 이를 바탕으로 운전자에게 경고하는 방식이다. 간접방식에 비교하여 시스템의 가격이 높으나 계측 값이 정확하고 시스템이 안정적이어서 대부분의 자동차에는 직접방식 TPMS가 적용되고 있다.[30]
차고센서 [ 편집 ]
하이트센서라고도 알려져 있는 차고센서는 노면으로부터 차량 높이를 측정하는 센서다. ECS의 핵심요소로, 주행 시 차량 바디와 차체 상대 위치, 특히 차고의 변화를 감지해 전자제어 현가시스템의 ECU에 정보를 제공한다. 현재의 차고 높이를 측정해 목표 차고보다 낮으면 저장 탱크의 압축공기를 에어스프링에 공급해 차체를 상승시키고, 목표 차고보다 높으면 압축공기를 대기로 방출시켜 차고를 낮춤으로써 항상 일정한 높이를 유지한다. 이 정보를 통해 노면이 울퉁불퉁한 비포장도로에서는 차 높이를 높여 차체를 보호하고, 고속주행이 가능한 도로에서는 차 높이를 낮춰 주행안정성을 높이는 역할을 수행한다.[31]
중력센서 [ 편집 ]
중력센서는 중력이 어느 방향으로 작용하는지 탐지하는 센서이다. 중력센서를 통해 차량 충돌시 방향을 기록할 수 있고 차의 진행방향과 가속도, 진동, 충격을 측정하는 등 평소 운전습관을 파악하는 데 도움이 된다.[32] 중력센서는 내비게이션에 사용된다. 위성을 통해 파악하는 GPS 좌표와 함께 중력센서로 차량의 회전방향을 동시에 분석한다. 이에 따라 차량이 내비게이션의 설정 경로를 이탈할 경우 중력센서가 이를 감지해 신속하게 경로 재탐색에 들어간다. 차량사고가 났을 때 원인을 규명하는 블랙박스에도 중력센서는 필수다. 중력센서가 흔들리면 자동으로 차량의 진행 방향과 진동, 충격을 측정할 수 있다.[33]
토크센서 [ 편집 ]
토크센서는 연속적으로 회전하는 축의 토크를 측정하는 센서이다. 회전 토크미터라고도 한다.[34] 토크센서는 EPS 시스템의 핵심부품으로 조향축에 걸리는 토크를 측정하여 EPS 제어기에 전달하는 역할을 한다. 토크(torque)란 어떤 것을 어떤 점 주위에 회전시키는 효과를 나타내는 양으로서, 회전 모멘트 또는 비틀림 모멘트라고도 부르며 회전체의 접선방향 힘의 크기와 힘이 걸리는 점에서 회전 중심점까지의 길이를 곱한 N·m 또는 kgf m 단위로 나타낸다. 토크 측정방식은 크게 접촉식과 비접촉식으로 구분된다. 접촉식 토크센서에는 슬라이딩 방식의 저항형 포텐션미터(potentiometer), 접촉식 스트레인 게이지, SAW 토크센서 등이 있으나 내구성이 떨어지고, 2바퀴 반 이상 회전하는 자동차 조향축에 실장하는데 부적합하기 때문에 자동차 토크센서로는 주로 비접촉식 토크센서를 사용한다. 비접촉식으로 자동차 분야에서 많이 사용되는 있는 기술은 자기식으로 자기장 형성 구조물과 고감도 자기센서를 사용한다. 자기식 토크센서는 샤프트 주위에 정해진 패턴의 자장을 형성시킨 상태에서 토크에 의해 회전 변위가 발생될 때 이에 따른 자기장의 변화가 발생하게 되고, 이를 자기센서로 측정하는 방식이다. 샤프트로부터 수 mm 이격하여 토크를 측정하며, 먼지나 액체 등 기타 비자성 물질이나 높은 회전 속도에서도 매우 잘 동작을 한다. 단점으로는 샤프트가 자화될 수 있으며, 강력한 자계 환경에 노출되어서는 안 된다. 장점을 보면 다른 비접촉식 회전센서에 비해 저가격으로 제작이 가능하고, 장착이 용이하면서도 자동보정 및 추가조정이 최소화될 수 있다. 에너지 소모가 적고, 내구성이 뛰어나며, 토크 측정은 물론 각도와 위치측정도 가능하다. 비접촉식으로 감지 샤프트, 신호감지부, 전자신호 처리부가 하우징에 내장되어 콤팩트한 자기식 토크센서의 개발이 가능하다. 자기식 토크센서 중 자동차용 조향 토크 측정에 적용되는 센서의 일례로, 스티어링휠 축에 부착되는 마그넷로터에서 발생하는 자기력에 의해 휠타이어 측 축에 연동한 고정자 치(stator tooth)에 1차 자기 유도되고, 회전하는 고정자 치에 유도된 자기력이 외부의 고정형 콜렉터(collector)로 2차 자기 유도되어 홀 IC 센서로 변화를 감지한다. 비틀림이 발생하면 로터와 고정자가 어긋나게 되어 자기장의 세기 변화가 발생하게 되는데, 일정범위 내에서 토크에 비례하는 자기장 변화가 발생한다.[35]
자율주행 센서 [ 편집 ]
자율주행 센서는 자차의 위치인식을 위한 센서와 주행 환경에 존재하는 다양한 물체인식을 위한 센서로 구성된다. 위치인식을 위해서는 관성측정센서(IMU), 위성항법센서(GPS), 카메라, 라이다 등이 사용되며, 물체인식을 위해서는 카메라, 라이다, 레이다 등이 사용된다. 자차의 정확한 위치 정보가 획득된다면, 고정밀 자율주행지도를 참조하여 실세계 좌표계에서 전역 경로계획을 세울 수 있다. 전역 경로계획으로 자율주행 하면서 자차의 주행 경로 주변에서 이동하거나 정지된 물체를 인식하여 지역경로계획까지 수립하고, 섀시 시스템의 종/횡방향 제어를 수행함으로써 자율주행이 실행된다. 이상과 같은 자율주행 자동차 시스템 구현을 위해서는 위치인식과 물체인식 기능이 필수적이고, 카메라와 라이다는 두 가지 기능에서 모두 사용되는 센서이므로 활용 범위 측면에서 중요성이 더욱 커지고 있다. 레이다 센서의 경우는 물체인식 기능에 한하여 사용 가능한 센서이나 열악한 주행 환경에서도 가장 신뢰성 있는 데이터를 제공할 수 있기 때문에 첨단운전자 지원시스템(ADAS) 시장에서 지속적으로 매출이 확대되고 있다.[36]
카메라 [ 편집 ]
카메라 센서는 첨단 운전자 지원 시스템 시장에서부터 이미 핵심 센서로 발전하였고, 향후 자율주행 시대에도 가장 큰 시장을 형성할 것으로 예측된다. 의무 장착으로 시장이 확대된 후방 감시 카메라, 모빌아이(Mobileye)가 개척한 다기능 전방카메라, 다임러(Daimler)가 견인하는 스테레오 카메라, 야간 감시 카메라와 운전자 모니터링 카메라까지 다양한 종류와 기능을 가진 카메라가 시장을 형성하고 있고, 자율주행 자동차에는 더 많은 종류의 카메라가 장착될 것으로 전망된다. 자율주행을 위한 카메라 조합은 테슬라(Tesla)의 새로운 오토파일럿 시스템에 장착된 8대 카메라 구조를 살펴봄으로써 향후 발전 방향을 조망할 수 있을 것이다. 테슬라의 오토파일럿은 전방 카메라 3개, 후방카메라 2개가 장착되어 총 8개의 카메라와 레이다, 초음파 센서로 구성되며, 센서 융합 플랫폼은 엔비디아(Nvidia)의 드라이브 PX2를 사용한다. 모빌아이와의 협력 관계를 청산하고 자사의 독자 카메라 솔루션을 개발한 테슬라는 원거리 전방과 360도 주변환경을 카메라 센서만으로 인지한다. 각 카메라의 검출 거리, 화각, 장착 위치 등을 고려하면 개별 카메라가 담당할 인지 기능을 예측할 수 있다. 공개된 정보에 의하면 8개의 카메라 기능이 완성된 것은 아니고, 향후 소프트웨어 버전을 개선하면서 새로운 기능을 추가해 갈 것으로 판단된다. 한편 자율주행 3단계에서는 자율주행 상태에서 운전자의 주의 집중이 요구되므로 운전자 상태 모니터링 기능이 반드시 필요하게 되어서 다양한 기업들이 운전자 모니터링 카메라 제품을 시장에 출시하고 있다.[36]
라이다 [ 편집 ]
자율주행 자동차에서 라이다(Lidar) 센서의 중요성이 부각되면서 기존의 업체들은 저가격화 및 소형화와 함께 자동차 전장 신뢰성이 확보된 양산 제품 개발을 진행하고 있고, 신규업체도 자율주행 자동차 시장에 도전하고 있다. 기존의 연구용 제품들은 대부분 3D 레이저 스캐닝 방식이기 때문에 소형화와 저가격화에 문제가 있었으나, 최근에는 광다이오드(photodiode)의 배열을 통해 광전 변환된 아날로그 신호를 증폭하는 3D 플래시 방식이 소개되면서 자동차 업계에서 양산 개발을 위한 투자를 집중하고 있다. 이베오 오토모티브 시스템즈(Ibeo Automotive Systems)를 인수한 프랑스 기업 발레오(Valeo)가 아우디(Audi) A8 차량에 세계 최초의 양산 레이다인 스카라(SCALA)를 출시할 예정이다. 스카라는 4채널의 스캔 라인으로 구성되며, 145도의 수평화각과 150미터의 거리를 40ms의 속도로 측정할 수 있다. 쿼너지시스템즈(Quanergy Systems), 테트라뷰(TetraVue) 등은 3D 플래시 방식의 라이다를 저가격으로 양산하겠다는 계획을 발표하과 있어서 향후 라이다 센서는 신기술 혁신과 가격 절감이 급격하게 이루어질 것으로 기대되고 있다. 국내에도 라이다 국산화 개발을 위한 정부와 민간투자가 이루어지고 있으나, 아직까지 자율주행 자동차에 적용될 수 있는 수준의 제품이 없어서 선진기업과의 기술격차 극복을 위한 노력이 절실한 상황이다.[36]
레이다 [ 편집 ]
레이다(Radar)는 2x GHz와 7x GHz의 밀리미터 파장을 이용하여 협대역 방식과 초광대역 방식으로 구분되어 검출 거리에 의해서 근거리, 중거리, 원거리 레이다로 나뉜다. 2x GHz 레이다는 주로 사각지대검출, 차선변경지원, 혼잡지역지원, 후방충돌경보 등의 기능을 제공하는 센서로 사용되고, 7x GHz 레이다는 해상도와 검출 거리 측면에서 장점이 있기 때문에 적응순항제어와 자동긴급제동 등에 사용된다. 각 나라의 안전 규제와 신차 안전도 평가 프로그램으로 인해 적응순항제어와 자동긴급제동 등을 위한 레이다 수요는 지속적으로 증가될 것으로 예측된다. 레이다 개발을 위해서 과거에는 밀리미터 파장의 신호처리를 위한 고주파 회로기술이 필요했으나, 최근에는 자동차용 반도체 기업들이 원칩 레이다 솔루션을 제공하고 있어서 저전력, 소형화 가격 절감이 가능하게 되었다. 글로벌 경쟁력을 가진 레이다 센서 기업은 보쉬(Bosch), 콘티넨탈(Continental), 덴소(Denso), 델파이(Delphi), 오토리브(Autoliv) 등이며 국내에서는 만도(Mando)가 유일하게 독자 레이다 개발 능력을 보유하고 있다.[36]
관련 네트워크 [ 편집 ]
자동차에서 센서 부분의 비중은 매년 증가하는 추세에 있다. 센서기술의 중요한 역할은 기본적으로 운전자 또는 전자제어시스템에 검지된 정보를 원하는 시간 내에 제공할 수 있어야 한다. 이러한 목적을 달성하기 위해 자동차에는 다양한 센서와 전자시스템이 결합되어 있다. 이런 분산된 센서와 전자시스템을 연결하는 데 사용하는 배선 장치는 엄청난 케이블을 필요로 하게된다. 이로 인해 전체적인 차량 무게가 증가하고 제조비용이 상승하게 된다. 이러한 문제를 해결하기 위해, 모든 센서 시스템을 차량 내에서 한 개 혹은 두 개의 전선으로 구성된 공통 네트워크 버스에 연결하여 사용되고 있다. 차량용 센서 정보를 제공할 수 있는 네트워크 프로토콜은 정보계와 제어계로 크게 나눌 수 있다. 정보계는 수 십 메가비트(Mbps)에서 수 백 메가비트를 지원하며, 제어계는 수 십 킬로바이트(kbps)에서 수 십 메가비트를 지원한다. 제어계는 전송 속도에 따라 다시 여러 용도로 구분하여 사용된다. 예를 들어 안전계는 수백 케이피에스(kbps)에서 10 메가비트 정도이며, 바디계는 수십 킬로바이트에서 1 메가비트 정도이다. 다양한 프로토콜이 차량용으로 특별히 고안되어 왔다. 가장 오래되고 잘 알려진 프로토콜은 CAN(캔)이며, 동력발생장치 애플리케이션에는 대부분 고속 CAN(CAN-A)을 사용한다. 차체 애플리케이션에는 저속 CAN(CAN-B)이 주로 사용된다. 달성 가능한 최고 데이터 속도는 1Mbit/s이지만 일반적으로 네트워크는 500kbit/s 이하에서 운영된다. 낮은 전송 속도를 요구하는 비용 효율적인 모듈용으로 개발된 LIN(린) 프로토콜은 이미 널리 사용되고 있다. 이 프로토콜이 지원하는 데이터 속도는 20Kbit/s로 특히 초음파센서, 우적센서, 조도센서 등과 같은 차체 애플리케이션용으로 사용되고 있다. 속도 면에서 볼 때, 플렉스레이(FlexRay)는 CAN 프로토콜과 MOST 프로토콜의 중간쯤에 위치하지만 이중화와 시간동기화 등에 따른 내결함성 기능으로 인해 다른 프로토콜보다 높은 안전성을 갖고 있다. D2B 프로토콜과 그 후속 기술인 MOST 프로토콜은 멀티미디어 애플리케이션용으로 특별히 개발됐으며, 전적으로 멀티미디어 분야에만 사용된다. 이 프로토콜은 센서 등과 같은 분야에 배치하기에는 적절하지 않다. 차량 전자장치들과 센서들이 급속히 늘어남에 따라 상호간에 더욱 빠르고 많은 정보를 교환할 필요성이 대두 되고 있으나, 기존 네트워크 기술로는 만족스러운 통신이 이루어지지 못하게 되어 상호간 통신 속도를 높여주는 고속 차량 네트워크 기술이 등장하고 있다.[2]
LIN [ 편집 ]
LIN(Local Interconnect Network)은 CAN보다 저렴하면서도 복잡하지 않은 센서, 액추에이터 등의 자동차 애플리케이션 요구를 지원하기 위해 개발되었다. LIN 규격은 LIN 컨소시엄에서 2010년 LIN 2.2 버전을 발표했다. LIN은 안전이 매우 중요시 되지 않는 센서 및 액추에이터 영역에서 시리얼 데이터 교환을 위한 저렴한 통신 프로토콜을 만들기 위하여 주로 물리계층의 설계에 영향을 미쳤다. LIN 클러스터에서 물리적인 신호 전송은 CAN에서 익숙한 차동 신호 전송을 포함하지 않으며 기존의 단일 선이 사용 된다. 이 방법에도 불구하고 노이즈 내성을 충분히 보장하기 위해 버스 레벨을 위한 기준 전압으로 엔진제어장치의 공급전압과 그라운드가 사용된다. LIN 트랜시버는 물리적 버스 인터페이스로 사용된다. 공급전압보다 적어 도 40% 낮은 레벨은 리시버에 의해 논리 “0”으로 해석된다. 리시버들은 적어도 공급 전압보다 60% 높은 레벨을 논리“1”로 해석한다. 최대 데이터 전송속도는 노이즈 방사를 한계 이내로 유지하기 위해 20 kbps로 한정되며, 전선의 길이 최대 40미터까지는 최대 추천 노드 수가 16개이다. 이것은 LIN 사양에서 규정한 LIN 클러스터의 최대 허용 편차를 포함한 노드와 라인의 커패시턴스를 고려하는 것이다. LIN 버스는 초음파센서, 온습도 및 우적센서, 조도센서 등 일반적으로 지능형 센서를 연결하는데 사용된다. 이런 애플리케이션에 있어서, 매우 높은 데이터 전송 속도나 복잡한 고장 관리는 필요하지 않다. 그리고 EMI 특성에 영향이 적은 속도와 성능을 유지하는 것이 최대 20kBit/s의 데이터 전송 속도를 지원하는 이유다. 전송 속도와 전송 매체에 따라 12V 싱글 와이어로 구성된다. LIN은 SCI(Serial Communication Interface)로서 8비트 인터페이스를 기반으로 하며 단일(마스터)와 다중(슬레이브) 개념을 지원한다. SCI 인터페이스는 거의 모든 마이크로컨트롤러나 에이식에서 지원되며, 어떤 소프트웨어나 펌웨어로도 구현할 수 있다. 이로 인해 다른 값비싼 외부 부품을 사용할 필요가 없다. 마스터 노드에서 마스터 및 슬레이브 태스크를 모두 수행하며, LIN 네트워크 내에 마스터를 제외한 노드는 다른 슬레이브를 추가하거나 제거해도 영향을 받지 않는다. 이런 경우에, 단지 필요한 변경은 마스터노드와 관련이 있다. LIN의 특별한 기능은 추가적인 크리스탈이나 공진기 없이 마스터로 슬레이브 노드의 클록 속도를 조정하는 동기화 메커니즘이다. 비용에 민감한 문제로 인해 LIN 슬레이브들은 주파수 허용오차가 최대 14%에 달하는 온칩 레조네이터를 사용할 수 있다. LIN 네트워크가 가능한 센서로서 차량용 초음파센서가 있다.[2]
CAN [ 편집 ]
CAN(Controller Area Network)은 자동차 내의 각종 계측제어 장비들 간에 디지털 시리얼 통신을 제공하기 위하여 1988년 보쉬와 인텔에서 개발한 차량용 네트워크 시스템으로, 1993년도에 ISO에서 국제표준 규격으로 제정되었다. 처음 개발된 것은 1986년 로버트 보쉬(Robert Bosch)에 의해서다. 최고 속도 125kBit/s까지의 활용을 위해 ISO 19898로 각각 표준화되었다.[37] CAN은 다른 자동화 통신망에 비해 가격 대비 성능비가 우수하며, 지난 수년간 차량 내의 열악한 환경에서 성공적으로 동작되어 신뢰도가 검증된 통신망이다. CAN은 마스터/슬레이브, 다중 마스터, P2P 등을 지원하는 매우 유연성 있는 네트워크이며 공장의 열악한 환경이나 고온, 충격이나 진동, 노이즈가 많은 환경에서도 높은 신뢰성을 제공한다. CAN에 의해 데이터가 교환될 때 어떠한 스테이션도 주소화 되지 않고 메시지의 내용은 통신망에서 유일하게 존재하는 메시지 식별자에 의해서 정해진다. 식별자는 메시지의 내용뿐 아니라 우선순위도 결정하는데, 이것은 여러 개의 스테이션이 동시에 버스를 액세스하려고 할 때 버스 할당을 위하여 중요하다. CAN에서는 콘텐츠 기반의 어드레싱 구조에 의해 구성의 융통성을 꾀할 수 있으며, 새로운 스테이션이 순수한 수신기라면 어떠한 하드웨어나 소프트웨어의 변경 없이 현존하는 CAN 통신망에 붙일 수 있다. 또한 데이터 전송 프로토콜이 물리적인 도착지의 주소를 필요로 하지 않기 때문에 모듈러 일렉트로닉스(modular electronics)의 개념을 지원하고, 또한 브로드캐스트나 멀티캐스트와 같은 다중수신과 분산처리의 동기화를 허용하여 여러 개의 컨트롤러에서 정보로 필요로 하는 측정값들이 통신망을 통해 전송될 수 있으므로 각각의 컨트롤러가 자신만의 센서를 가지고 있을 필요가 없다. CAN은 멀티 마스터 통신이므로 어느 노드에서도 통신을 개시할 수 있다. 다만 실제로 하나의 버스 상에서 동시에 수행할 수 있는 통신은 하나뿐이다. 각 노드는 버스 상태가 송신 중인지 아닌지를 주기적으로 확인한다. 그리고 버스 상에서 송신이 이루어지지 않는 경우에 통신을 개시하지만, 복수의 노드가 송신을 개시하면 충돌한다. 이때 CAN에서는 조정을 하여 아이디가 작은 것을 우선 송신함으로써 충돌을 피하고 있다.[2] CAN은 오랫동안 자동차의 엔진제어장치를 접속하는 주요 버스 기술로 사용돼 왔다. 하지만 자동차에서 필요한 데이터 전송 속도를 CAN에서는 기대할 수 없는 대상이 개발되자, 이보다 빠른 전송 속도를 갖는 시간 결정적 프로토콜이나 다수의 고장 방지 시리얼 버스 시스템의 개발이 이루어졌다. 예를 들면 TTCAN(Time Triggered CAN) 등이 있다. CAN 네트워크가 가능한 센서로서 차량용 요레이트센서가 있다.[38]
플렉스레이 [ 편집 ]
플렉스레이(FlexRay)는 비엠더블유(BMW)에서 개발한 통신 시스템인 바이트플라이트(byteflight)를 기반으로 하고 있다. 바이트플라이트 방법은 새로운 버스 시스템의 요구 조건을 만족시키기 위해, 순차 결정(chronological deterministic) 및 결함 허용(Fault Tolerance)에 대한 개선이 이루어졌다. 플렉스레이의 10-Mbit/s 대역폭, 내재된 결함내성 그리고 결정 프로토콜이 적용되었다. 또한, 다중 네트워크 토폴로지도 지원할 수 있도록 만들었다. 확장성을 고려하여 설계된 플렉스레이는 향후 새로운 기술적 요구 사항들에 대해서도 대처 가능할 것으로 보고있다. 플렉스레이는 안전성 고려와 혹독한 작동 환경에 요구되는 강건함, 이중화된 네트워크를 통한 고신뢰성, 동기화된 시간축에 따른 고정밀 등과 같은 특징을 가지고 있다. 네트워크 플렉스레이는 기존 차량용 네트워킹 시스템에 비해 비약적인 발전을 했다. 그러나 IC 설계 관점에서 플렉스레이의 진보된 특징들은 트랜시버와 통신 컨트롤러를 10년 이상 설계해온 엔지니어들의 노하우가 기반이 되고 있다. 따라서 차량용 시스템 IC 부문은 진입장벽은 높으며, 매우 소수의 IC 회사들만이 시장에 성공적으로 진입한 것이다. 플렉스레이는 최대 대역폭 10Mbit/s로 데이터를 전송하므로 실시간 동작용으로 아주 적합하다. 더욱이 플렉스레이는 버스, 스타, 종속형 스타(cascaded star), 하이브리드 네트워크 토폴로지 등 다수의 네트워크 토폴로지들을 지원한다.[37] 그리고 CAN이 CSMA를 지원하는데 비해 플렉스레이는 TDMA(Time Division Multiple Access)를 지원한다. 따라서 어떤 장치가 버스에 대해 배타적 액세스 권한을 가지고 있는 동안 각 장치는 고정된 시간창(타임 슬롯)을 가지고 있다. 이런 타임 슬롯은 고정된 패턴을 가지고 정의된 간격으로 반복된다. 그래서 TDMA를 이용하면, 데이터가 버스 상에 있는 시간을 정확히 예측할 수 있다. 모든 노드들은 이런 종류의 통신을 적절하게 처리하기 위해 같은 전역 시간을 가지고 있다. 플렉스레이 네트워크가 가능한 센서로서 차량용 요레이트센서가 있다.[2]
시장 [ 편집 ]
차량용 센서 시장은 2020년 281억 달러에서 2025년 419억 달러로 확대되고, 연평균 성장률은 6.9%로 예측된다. 자동차 내 센서는 속도나 위치, 압력, 온도와 같은 여러 변수에 대한 데이터를 수집하여, 전자 제어 장치에 제공한다. 이렇게 수집된 데이터는 차량의 안정성과 편의성 개선에 도움을 주기 때문에 자동차에 있어 센서는 필수적이다. 최근 대체연료 차량 및 전기자동차의 증가, 배출 표준 및 안전에 관한 정부의 규제 엄격화가 센서 시장의 성장을 이끄는 주된 요인이다. 자동차 한 대에 사용되는 센서는 약 200여 개에 이른다. 주행보조장치 장착 차량의 증가와 자율주행차 관련 R&D의 확대로 차량의 내부뿐만 아니라 외부의 환경변화에 대해 더욱 정확한 인식과 정보전달이 가능한 차량용 센서의 필요성도 커지고 있다. 이를 바탕으로 자동차에서 사용되는 센서의 수와 종류가 증가하며, 차량용 센서 시장도 계속 성장할 전망이다.[39]
각주 [ 편집 ]
참고자료 [ 편집 ]
같이 보기 [ 편집 ]
자동차 센서 정리
2.1 엔진 전자제어 시스템
엔진 전자제어 시스템은 ECU로 엔진의 모든부분을 총괄하는 역할을 한다.
전자제어식 연료분사장치는 기관의 회전속도와 흡입 공기량, 흡입공기 온도, 냉각수 온도, 대기압, 스로틀밸브의 개도량 등의 상태를 각종 센서로 감지하여 electronic control unit (ECU)에 전자 신호로 입력 시킨 후 기관의 운전조건에 가장 적합한 혼합기로 만들기 위해 인젝터를 통해 연료를 흡기다 기관 내에 분사시킨다.
2.2 전자제어식 연료분사장치의 입출력요소
2.2.1 공기유량센서 (air flow sensor)
엔진으로 유입되는 공기량을 검출하여 ECU로 전달한다. ECU는 이 신호를 받아 연료 분사량을 결정하고, 분사 신호를 인젝터로 보내 연료를 분사시킨다.
공기 유량 센서의 종류에는 흡입 공기량 계측 방식인 에어플로미터식(베인식), 칼만 와류식, 열선식 등과 흡입 압력 검출 방식인 MAP 센서가 있다.
2.2.1.1 에어플로미터 (air flow meter)
에어플로미터는 에어클리너 안에 설치되어 있어 흡입공기의 양을 베인형식의 미저링 플레이트가 측정하고 포텐셔미터가 정압비로 변화시켜 ECU로 신호를 보낸다. ECU는 크랭크 전 앵글센서의 엔진 RPM신호와 에어플로미터의 흡입공기량 신호를 기초로 하여 분사량을 결정한다.
2.2.1.2 열선식 공기유량센서 (hot-wire air flow sensor)
열선식 공기 유량 센서는 흡기의 온도, 압력, 밀도와는 상관없이 엔진에 유입된 흡기질량을 직접 계측한다. 따라서 외부의 온도나 고도 등에 영향을 받지 않는 특성이 있다. 따라서 대기압 센서나 흡기온 센서를 생략할 수 있는 장점이 있다.
열선이 흡기 통로에 설치되어 있기 때문에 열선에 오염물질이 잘 퇴적된다. 오염물질이 퇴적 될 경우 측정결과에 오차가 생기게 되므로 이를 방지하기 위해서 엔진이 정지되면 열선을 약 1,000℃ 정도로 가열하여 순간적으로 퇴적물을 연소, 제거시킨다. 이것을 클린 버닝(Clean burning)이라고 한다.
2.2.1.3 열막식 공기유량센서 (hot-film air flow sensor)
열막식 공기량 센서는 열선식 공기 유량 센서를 대체할 목적으로 개발된 센서이다. 열선식 공기 유량 센서 백금열선, 온도센서, 정밀저항 등으로 구성되어 있어서 생산비용이 높은 편이었다. 열막식 공기 유량 센서는 백금열선, 온도센서, 정밀저항 등으로 구성되어 있어서 생산비용이 높은 편이었다. 열막식 공기 유량 센서는 이 세가지 부품을 세라믹 기판에 층 저항으로 집적시켰다. 또 열막 센서(Hot film resistor)가 공기의 유동방향과 일치하여 설치되므로 열선식에 비해 오염에 덜 민감하다. 따라서 클린 버닝을 할 필요가 없고 생산비가 저렴하며 응답성도 좋은 장점을 지닌다.
2.2.1.4 칼만와류식 공기 유량 센서 (karman vortex air flow sensor)
공기가 흐르는 통로에 기둥을 세우면 그 기둥 뒤에는 규칙적인 소용돌이가 발생하는데, 이 와류현상을 칼만 와류라고 한다.
이러한 칼만 와류를 이용하여 와류 발생부에 초음파를 송신한 후 와류에 의해 변화된 초음파를 수신하여 변조기에 의해 디지털 신호로 변화되어 ECU에 입력된다.
2.2.2 MAP센서 (manifold absolute pressure sensor)
MAP센서는 직접 흡기다기관내 설치되어 흡입매니폴드의 압력 변화를 전압으로 변화시켜 ECU로 신호를 보낸다. ECU는 이 신호에 의해서 엔진의 부하 상태를 판단할 수 있고 흡입공기량을 간접 계측할 수 있으므로 연료분사시간을 결정하는 주 신호로 사용된다.
많이 사용되는 형식으로는 후막–압력센서와 반도체–압력센서가 있다.
2.2.2.1 후막 압력센서(Thick-film pressure sensor)
후막 압력센서는 흡기다기관에 설치되거나, ECU에 설치된다. ECU에 설치된 경우에는 호스를 통해 센서에 흡기다기관의 부압이 작용하는 구조로 되어 있다.
2개의 센서–엘리먼트가 설치된 압력실 그리고 평가회로가 설치된 부분으로 구성되어 있다. 센서–엘리먼트와 평가회로는 1개의 공통 세라믹 기판에 설치되어 있다. 그리고 압력실에는 흡기다기관 절대압력(MAP)이 작용한다.
MAP–센서의 압력실에는 세라믹기판 위에 약간 볼록한 두꺼운 막이 접착되어 있고, 막 안에는 기준압력이 밀폐되어 있다. 그리고 막 외부에는 압전저항소자가 부착되어 있다. 이 압전저항소자는 흡기다기관의 압력이 변화할 때, 막의 기계적 팽창도의 변화에 따라 저항값이 변화한다. 저항값이 변화함에 따라 전압신호도 변화한다.
K–계수(상대 저항변화/팽창도)가 12~15범위일 경우, 최대 약 20bar까지 측정할 수 있다. 평가회로는 전압신호를 증폭시키고, 온도영향을 보상하여, 선형화된 전압신호를 생성한다.
MAP–센서의 특성곡선은 공전 시 약 0.4V 그리고 고속에서 약 4.6V의 신호전압을 발생시킨다. 바로 이 두 전압값의 사이가 MAP–센서의 선형 작동영역이다. 엔진 ECU의 평가회로는 흡기압력신호 외에도 엔진회전속도 그리고 다른 여러 가지 신호들을 종합, 평가하여 필요한 분사시간을 결정한다.
2.2.2.2 반도체압력센서 (Semi-conductor pressure sensor)
반도체 압력센서의 형식은 대부분 압력변환 소자와 소자의 출력신호를 증폭하는 하이브리드 IC가 1개의 하우징에 집적되어 있으며 압력변환 소자로는 반도체의 압전저항효과(Piezo effect)를 이용한 실리콘 다이어프램 형식이 주로 사용된다.
센서는 흡기다기관에 직접, 또는 ECU나 엔진룸에 설치된다. 어떠한 경우에도 600℃ 이상의 온도에 직접적으로 노출되어서는 안되며, 작동온도범위가 150℃ 이하가 되는 위치에 설치하여야 한다. 압력이 작용하는 부분인 실리콘 다이어프램의 한 쪽은 진공 때문에 검출압력이 높을수록 실리콘 다이어프램의 변형(10~1000μm)이 크게 된다.
이 수축을 실리콘 다이어프램에 부착되어 있는 저항에 의해 휘스톤브릿지(wheastone bridge)에서 전기 신호로 변환시킨다. 이 전압신호는 미소하므로 하이브리드 IC를 이용하여 증폭시킨다.
반도체 압력센서는 흡기다기관 절대압력의 변화에 대하여 직선적으로 비례하는 전압을 발생시킨다.
2.2.3 흡기온도센서 (air temperature sensor)
공기유량센서 AFS에 부착되어 흡입한 공기의 온도를 검출하는 일종의 가변저항기인 부 특성 셔미스터이다. ECU는 센서로부터 출력전압에 의해 흡입 온도를 검지하여 흡입된 공기의 온도에 대응하는 연료량을 보정한다.
2.2.4 대기압센서 (barometric pressure sensor)
대기압센서(BPS)는 공기유량센서(AFS)에 부착되어 자동차가 위치한 지역의 대기압력을 측정해 ECU로 신호를 보낸다. ECU는 이 신호를 이용해 차의 고도를 계산하여 적정한 공연비가 되도록 연료 분사량과 점화 시기를 조정한다.
대기압 센서는 스트레인 게이지의 저항값이 압력에 비례하여 변화하는 것을 이용하여 압력을 전압으로 변환시키는 반도체 피에조(piezo) 저항형 센서이다.
그러나 우리나라 에서는 고지대가 많이 없기 때문에 칼만 와류방식에서도 사용을 잘 안하는 편이다.
2.2.5 스로틀 바디 (throttle body)
스로틀바디는 운전자의 가속의지(가속페달을 밟고 떼는 것)에 따라 스로틀밸브를 제어하여 엔진으로 흡입되는 공기의 양을 조절하는 흡기계통(Air intake system)의 구성부품을 말한다. 일반적으로 에어클리너와 흡기매니폴드 사이에 설치되며, 스로틀바디의 앞쪽 부분에는 흡입공기량센서가 부착되어 있다. 또, 대부분의 스로틀바디에는 스로틀밸브의 위치를 검출하는 스로틀밸브위치센서(TPS)와 공회전 속도를 조절하는 ISA(Idle speed actuator)가 설치되어 있다.
대부분의 자동차의 경우, 가속페달과 스로틀바디는 스로틀케이블에 의해 기계적으로 연결되어 있어서 스로틀밸브는 케이블에 의해 직접적으로 개폐되도록 되어 있다.
반면에 ETC(Electronic throttle control) 방식의 스로틀바디에서는 운전자가 가속페달을 밟으면 먼저 페달에 부착되어 있는 엑셀레이터 위치센서(APS, Accelerator position sensor)가 페달의 위치(변화량)를 검출하여 ECU로 보낸다. ECU는 이를 기준으로 다른 입력신호와 함께 스로틀밸브의 열림량을 연산하여 스로틀바디에 부착된 모터를 구동시켜 엔진의 작동상태에 적합한 스로틀밸브의 개도를 변화시키게 된다. 즉, 스로틀밸브의 개도는 전기적 신호와 모터에 의해 변화된다. 이와 같은 구동방식을 Drive-by-wire 라고 한다.
2.2.5.1 스로틀밸브위치센서 (Throttle position sensor)
스로틀밸브위치센서(TPS)는 스로틀바디에 장착되어 있으며, 스로틀밸브의 개도를 감지하는 기능을 한다. 스로틀밸브 축에 고정된 슬라이더 암이 저항레일에 접촉된 상태로 미끄럼 운동을 하는 구조이다.
운전자가 가속페달을 밟으면 페달에 연결된 엑셀러레이터 케이블에 의해 스로틀밸브 축이 회전운동을 하게 되고, 이 회전운동으로 인하여 슬라이더암이 저항레일에 접촉된 상태로 미끄럼운동하면서 저항값을 변화시키게 된다. ECU는 저항레일에서의 전압강하로부터 스로틀밸브의 개도를 인식한다. ECU는 이 전압 변화를 기초로 하여 엔진의 가속 상태를 판단하고 그에 따라 필요한 제어를 실행한다.
2.2.5.2 대시포트 (dash pot)
대시포트의 기능은 차량이 일정속도로 주행을 하다가 감속을 위해 엑셀레이터페달에 발을 떼었을 때, 스로틀배릅가 급격히 닫혀 차량감속으로 인해 오는 충격과 배출가스를 적당히 유지하기 위하여 스로틀밸브가 완전히 닫히기 전에(1500 ~ 2000rpm) 약 0.5초간 서서히 스로틀 밸브를 닫아주는 작용을 말한다.
2.2.6 산소센서 (oxygen sensor)
산소센서는 배기가스 중의 산소와 대기 중의 산소 농도 차에 따라 이론공연비(14.7 : 1)를 중심으로 출력전압이 급격히 변화되는 것을 이용하여 피드백의 기준신호를 공급해주는 역할을 한다. ECU는 이 신호를 이용해 인젝터 열림 시간을 제어해 연료 분사량을 조정한다.
산소센서는 소자의 종류에 따라 지르코니아 센서와 티타니아 센서2종류가 있다. 현재 일반적으로 사용되고 있는 것은 지르코니아 센서이다. 이 센서의 특징은 경시 변화에 의한 특성변화가 적다는 점이다.
2.2.6.1 지르코니아 산소센서 (zirconia oxygen sensor)
고체 전해질의 지르코니아 소자 (ZrO2)의 양면에 백금 전극을 설치하고 전극을 보호하기 위하여 전극 외측을 세라믹으로 코팅한 다음 센서의 안쪽에는 산소 농도가 높은 대기와 접촉되어 있고 외측에는 산소 농도가 낮은 배기 가스가 접촉되도록 하여 대기 측의 산소 농도와 배기가스 측의 산소 농도 차이에 의해 기전력이 발생되는 원리를 이용하여 산소 농도를 검출 한다. 지르코니아 산소센서의 출력은 공연비가 농후한 경우에는 배기가스 중의 산소농도가 적으므로 농도차이가 커져 전위차가 크고, 희박한 경우는 배기가스 중의 산소 농도가 많으므로 농도 차이가 작아 전위차가 적다.
2.2.6.2 티타니아 산소센서 (titanic oxygen sensor)
티타니아 산소센서 세라믹 팁에 티타니아 소자를 설치하여 전자 전도체인 티타니아가 주위의 산소 분압에 대응하여 산화 또는 환원되어 전기 저항이 변화되는 것을 이용하여 산소농도를 검출하는 방식이다.
지르코니아 센서에 비해 작고 내구성이 좋지만, 값이 비싸고 온도에 대한 저항치 변화가 큰 결점이 있기 때문에 보정회로를 추가해 사용해야 한다는 단점이 있다.
2.2.7 냉각수온 센서 (water temperature sensor)
인젝터를 통해 분사된 연료는 온도가 높을 경우 연소가 잘된다.하지만 냉각된 상태에서는 연료를 무화 상태로 분사 하더라도 연료들간에 서로 뭉치는 현상이 발생하여 완전연소를 시킬 수 없으며 냉간 시동이 어렵다
냉각수온 센서(WTS)는 이러한 이유로 인해 흡기매니폴드의 냉각수 통로에 설치되어 냉각수온을 검출하는 일종의 가변저항기이다.
온도변화에 따른 출력전압의 값을 ECU로 보내 ECU는 이 신호로 엔진의 난기 상태를 판정하여 엔진이 냉각상태일 때 연소를 원활하게 하고 시동성을 좋게한다.
냉각수 온도에 따른 엔진의 RPM도 제어한다.
2.2.8 노크센서 (knock sensor)
엔진의 효율 향상을 위해서는 엔진의 압축비가 높아야 한다. 하지만 압축비가 상승하면 연소최대 압력이 증가하여 엔진의 효율이 좋아지지만 노킹의 발생 가능성도 높아진다.
노킹이란 엔진의 이상연소로 인한 것으로 엔진의 정상적인 연소는 점화불꽃에 의하여 혼합기가 착화되고 착화된 화염면이 전파되면서 이루어진다.
그런데 화염면이 정상적으로 도달되기 전에 국부적으로 자기착화에 의해 급격히 연소가 이루어지는 경우가 있다. 이 이상연소로 인해 발생하는 급격한 압력상승 때문에 실린더 내의 가스가 진동하여 충격적인 타격음을 발생시키게 되는데 이것이 노킹이다.
노크센서는 피에조소자를 이용하여 엔진연소 중 발생되는 진동을 전기신호로 바꾸어 ECU로 보내 주게 되며 ECU는 이 신호를 이용하여 노킹이 발생하는지 안하는지를 판단하게 된다.
노크가 발생되었다고 판단하게 되면 ECU는 점화시기를 지각시켜 노크를 저감시키게 된다.
노크센서는 구조 및 작동원리에 따라 전자유도식 노크센서와 압전식 노크센서로 나뉜다.
2.2.8.1 전자유도식 노크센서
전자유도식 코일 속에 철심을 넣고 철심의 끝 면 가까이에 진동자(Vibrator)를 설치하고 철심과의 사이에 작은 틈새(Air gap)를 만든 구조이다.
실린더 블록의 진동에 의하여 진동자가 진동하면 진동자와 철심의 틈새가 변화하여 자지 저항이 변하므로 코일속의 자속도 변화하고, 전자유도의 원리에 의해 코일에 기전력이 발생하게 된다.
이 때, 진동자의 고유진동수를 엔진의 노킹시에 발생하는 실린더 블록의 진동수와 일치시키면 노킹시에 최고로 진동자가 공진하여 코일에 커다란 교류전압이 발생한다.
2.2.8.2 압전식 노크센서
압전식 노크 센서는 힘이나 압력, 기계적 진동을 받으면 전압을 발생시키는 압전소자의 압전효과(Piezo Electric Effect)를 이용한 것으로, 공진형과 비공진형이 있다.
공진형 노크는 센서 본체와 진동자 사이에 압전소자를 끼워놓고 진동자의 진동이 압전소자에 가해져 진동을 전압으로 변화시키는 것이다.
진동자는 노크 진동과 거의 같은 공진 주파수를 가짐으로써 노킹 발생시 커다란 전압을 발생시키는 특징이 있다.
비공진형 노크 센서는 진동자가 없이 압전소자로부터 직접 전압을 검출하는 것이다.
2.2.9 캠 각 센서 (camshaft angle sensor)
피스톤의 상사점을 감지한다고하여 상사점센서 또는 TDC센서라고도 한다.
캠 각 센서는 캠축의 위치를 검출하는 센서로, 크랭크 각 센서와 동일 기준점으로 하여 크랭크 각 센서에서 확인이 불가능한 개별 피스톤의 위치를 확인할 수 있게 한다.
일반적으로 1개의 실린더헤드에 하나의 캠앵글센서가 설치되지만 가변밸브타이밍(VVT) 시스템에서는 흡배기 캠축에 하나씩 2개가 설치되기도 한다. 캠축에 별도의 센서휠을 두거나 캠기어 자체를 기준점으로 두어, 센서에 의해 캠축의 위치를 감지한다. 종전에는 발광소자와 수광소자를 활용한 옵티칼 방식의 캠 각 센서가 주류를 이루었으나 현재는 사용되지 않고, 홀효과(Hall effect)를 이용한 홀센서 방식이 이를 대체하고 있다.
크랭크 각 센서로 각 실린더별 피스톤의 위치는 알 수 있다. 하지만 이 피스톤이 어느 행정 중이냐는 알 수가 없다. 예를들어 4행정 1사이클 엔진에서 1, 4번 실린더의 피스톤과 2, 3번 실린더의 피스톤은 항상 동일한 높이(위치)에서 움직인다. 따라서 1번 피스톤이 압축행정에서 상사점 위치에 있는지 배기행정에서의 상사점 위치에 있는지 까지는 알 수가 없는 것이다.
캠 각 센서가 1번 실린더의 현재 위치가 압축행정에서의 상사점이라고 표시해주면 자동적으로 4번 실린더의 피스톤은 배기행정에서의 상사점 위치에 있게 되는 것이므로 ECU는 비로소 실린더별 피스톤의 정확한 행정과 위치를 알 수 있게 된다. ECU는 캠 각 센서와 크랭크 각 센서의 신호를 비교해서 1번 실린더의 압축상사점을 정확하게 파악해야 해당 실린더의 점화코일 또는 인젝터를 정확하게 트리거링 시킬 수 있다. 이와같이 캠 각 센서는 크랭크 각 센서를 통해 ECU가 점화시기 및 분사시기를 결정하는데 필요한 기준을 제공하는 역할을 한다.
캠 각 센서의 경우 크랭크 각 센서가 고장 났을 경우, 엔진의 회전속도 연산에 이용되기도 한다. ECU는 하나의 센서가 고장인 경우 이를 대체하여 다른 센서 신호로 고장난 센서의 값을 예측하거나 연산하는 보완적 모드를 운용하는데, 이것을 페일 세일프(Fail safe) 또는 림프 홈(Limp home) 모드라고 한다.
2.2.10 크랭크 각 센서 (crank angle sensor)
크랭크 각 센서(CAS)는 상사점에 관련된 크랭크샤프트의 위치(피스톤의 위치)를 감지하는 센서로서, 디스트리뷰터 내에 내장되어 있는 방식과 플라이휠에 부착된 방식이 있으며, ECU는 이 센서에서 나오는 신호를 기초로 하여 연료 분사시기를 결정하고 엔진 1회전당 흡입 공기량, 점화 신호 시기 등을 계산한다.
크랭크 각 센서의 종류로는 발광소자와 수광소자를 이용한 옵티칼(Optical) 방식, 자석을 이용한 인덕티브(Inductive) 방식, 홀소자(Hall IC)를 이용한 홀센서 방식 등이 있다.
2.2.10.1 인덕티브 방식 (Inductive type)
마그네틱 타입 이라고도 한다. 구조는 영구자석과 구리코일이 감긴 철심으로 구성되어 있으며 크랭크축에는 철-자성체의 센서 휠이 고정되어 있다.
크랭크축과 함께 센서 휠이 회전하면 센서 코일의 자속이 변화하고 이로인하여 교류전압이 유도된다. 센서 휠은 제어 시스템에 따라 돌기가 20~60개 정도로 구성되며, 일반적으로 피스톤의 상사점을 표시하기 위해 돌기 중 1~2개를 생략한다. 이와같이 돌기가 생략된 부분을 미싱투스(Missing tooth)라고 하고 센서 휠의 회전 중 미싱투스를 만나게 되면 인덕티브 센서에서 유도되는 전압 파형이 왜곡된다.
센서 휠의 간극이 큰 부분이 인덕티브 센서 앞을 지나갈 때는 간극이 작은 부분에 비해 자속의 변화가 크기 때문에 큰 펄스(전압)가 유도된다. 이 큰 펄스의 전압신호는 회전속도 계측을 위한 신호에 비해 주파수는 적다. 이 큰 펄스 신호가 크랭크축의 특정 위치(예 : BTDC 15°)를 나타내는 신호로서 ECU에서 연료분사시기 및 점화시기를 결정하는 데 사용된다.
그리고, 엔진의 회전속도가 느릴 때는 발생전압도 작고, 주파수도 적은 전압 파형이 유도되고, 회전속도가 빠를 때는 발생전압과 주파수 모두 큰 전압 파형이 유도되는 특징이 있다.
2.2.10.2 홀센서 방식 (hall sensor type)
홀(Hall)센서는 홀 효과를 이용한 전자 스위치로서 펄스발생기로 이용된다. 이 센서의 장점은 인덕티브 센서에서와는 다르게 신호전압의 크기가 엔진의 회전속도와 관계없이 일정하기 때문에 아주 낮은 회전속도도 감지할 수 있다. 또, 전압 파형이 디지털 타입이므로 ECU에서 별도의 신호처리(AC-DC 컨버팅)를 할 필요가 없다. 센서 휠의 구조 및 설치 위치는 인덕티브 방식과 동일하며, 구조도 유사하다.
홀센서는 홀전압 발생기, 영구자석, 평가회로 등으로 구성되어 있다. 평가회로는 2개의 홀전압 발생기(Hall effect element)의 홀전압을 평가하고 센서전압을 증폭시키는 기능을 한다. 센서 휠이 홀센서 앞을 지나가면 센서 휠의 위치에 따라 자장이 변화한다. 따라서 홀전압 발생기에 영향을 미치는 자장이 변화하고, 그렇게 되면 홀전압이 변화하게 된다.
2.2.11 공회전속도조절장치 (idle speed controller)
ISC 시스템은 아이들 상태에서 부하에 의해 떨어진 엔진 출력만큼 흡입되는 공기량을 증가시켜 엔진출력 부족으로 발생할 수 잇는 엔진부조 현상을 방지하는 장치이다.
ISC 시스템은 크게 2가지로 나눌 수 있다.
첫 번째로 엔진부하에 의해 떨어진 출력만큼 스로틀 밸브를 강제로 열어 흡입되는 공기량을 증가시킴으로써 엔진의 출력을 향상 시키는 방식이 있다.
두 번째는 스로틀밸브가 닫힌 상태에서 그것을 바이패스하는 공기통로로 공기를 추가 공급해 떨어진 출력만큼 공기량을 보상하는 바이패스 에어 방식이 있다.
요즘 나오는 차들은 거의 대부분 바이패스 에어방식을 적용하고 있다. 바이패스 방식은 또한 ISC 모터 방식과 스텝모터 방식의 2가지로 나눌 수 있다.
즉 제어방식에 따라 튜비제어 방식(ISC 모터방식)과 스텝 수 제어방식이 있는데, ISC 모터방식은 듀티 30~40 이고, 스텝모터는 4~14 스텝상태가 공전상태때의 규정값이다. 하지만 부하 신호에 따라 듀티값과 스텝값은 늘어나도록 되어있다.
2.2.11.1 공회전 스위치 센서 (idle switch sensor)
스로틀 보디에 독립적으로 설치된 방식과 TPS에 내장된 방식이 있다. 모두 접점식이며 스로틀 밸브가 공전상태에 있으면 ON신호가 ECU로 입력된다. ECU는 이 신호에 의해 적정한 공전상태를 제어하게 된다.
아이들 스위치가 정상적으로 작동하지 않을 때에는 가속불량으로 이어질 수도 있고, AT의 경우는 기어 변속상태가 잘 이루어지지 않을 수도 있다. 만약 아이들 스위치 신호 ON/OFF가 정상적으로 작동되지 않을 때에는 정확한 연료분사를 하지 못해 차가 가속순간 즉 비동기 분사가 이루어지지 않아 순간적으로 가속상태가 나빠지기도 한다.
2.2.11.2 에어컨 스위치와 릴레이 (air-con switch and relay)
에어컨 스위치는 에어컨의 ON·OFF 신호를 컴퓨터에 입력하여 에어컨을 ON시키면 ISC 서보를 작동시킴으로써 엔진의 공회전수를 설정값까지 상승시키며, 에어컨 릴레이는 컴퓨터에 의해 제어되어 에어컨 압축기에 축전지 전원을 ON·OFF시키는 스위치 역할을 한다.
또한 급가속하는 순간 5초 동안 에어컨 릴레이 회로를 차단하여 양호한 가속 성능을 유지시키는 구실을 한다.
2.2.12 차속센서 (vehicle speed sensor)
차속센서(VSS)는 자동차의 속도를 측정하기 위한 센서로, 그 신호는 속도계 외에도 전자식 자동 변속 장치나 미끄럼 방지 장치, 오토 드라이브 장치, 자동 도어 로크 장치, 차량 속도 경보 장치 등 각종 전자 장치에 이용되고 있다.
차량 속도 센서에는 기계식과 전기식이 있는데, 기계식은 오직 속도계에만 쓰이는 데 반하여, 전기식은 속도계와 전자 장치 양쪽에 사용되고 있다.
기계식에서는 트랜스미션 출력축의 회전을 플렉시블한 축에 의해 속도계의 구동축까지 전달하여 지침을 움직인다.
전기식에서 전자 픽업, 홀 소자, 리드 스위치, 자기 저항 소자 등을 이용하여 트랜스미션 출력축의 회전을 검출하고 있다.
위의 센서는 모두 바퀴 속도에 대응한 속도를 검출하고 있어서 바퀴가 로크(lock)되거나 슬립(slip)하고 있을 경우에는 차체의 속도가 다른 값을 나타낸다.
그래서 참된 차체의 속도를 검출하기 위해서 레이저나 초음파를 이용하여 대지(對地) 속도를 측정하는 것도 시도되고 있다.
2.2.12.1 리드 스위치식 차속 센서 (reed switch type vehicle speed sensor)
리드 스위치식 차속 센서는 스피드미터(속도계) 내의 회전자석 부근에 장착되거나 리드 스위치에 의해 차속에 비례한 회수의 ON, OFF 신호를 만들고 차속을 검출한다.
2.2.12.2 광전식 차속 센서 (photoelectric vehicle speed sensor)
광전식 차속 센서는 스피드미터 내의 발광 다이오드와 포토트랜지스터를 대향시켜서 조합하는 포토커플러와 스피도미터 케이블로 구동되는 차광판(날개차)에 의해 차속을 검출한다.
스피드미터 케이블의 회전에 의해 발광 다이오드 빛이 차단되며, 이로 인해 포토트랜지스터가 ON, OFF가 되어 신호가 만들어진다.
2.2.12.3 전자식 차속 센서 (Electronic vehicle speed sensor)
전자식 차속 센서는 리드 스위치식 차속 센서나 광전식 차속 센서와는 달리 트랜스미션에 설치되어 있고, 마그넷과 IC가 내장되어 있다.
트랜스미션에 스피드미터나 미터 드블링 기어의 회전은 회전축을 통하여 마그넷으로 전달되고, 마그넷의 회전은 자계의 변화를 일으킨다. 이것을 IC로 감지하여 차속을 검출한다.
2.2.12.4 전압 검출형 차속 센서 (voltage detection type vehicle speed sensor)
발전기의 발생 전압이 회전수에 비례하는 특성을 이용하여 전압을 검출하는 것을 말한다.
즉, 영구 자석이 케이블과 연결되어 회전하면 고정되어 있는 스테이터 코일에 교류 전압이 유기되고 정류기에 의해 직류 전기로 바꾸어 컴퓨터에 입력하여 연료 분사량을 조절한다.
또한 오버 드라이브 장치의 차속 센서로도 이용된다.
2.2.12.5 주파수 검출형 차속 센서 (cycle detection type vehicle speed sensor)
주파수에 비례하는 전압의 변화를 바꾸어 자동차의 속도를 검출하는 형식이다.
추진축 등의 회전부와 연결한 기어에 펄스 픽업을 접근시켜 회전하면, 기어의 끝이 펄스 픽업 쪽으로 접근하거나 멀어질 때 펄스 픽업은 회전수에 비례하는 주파수의 교류 전압이 발생된다.
이때 발생된 교류 전압을 직류 전압으로 바꾸어 컴퓨터에 입력해 연료 분사량을 조절한다.
자동 변속기의 차속 센서에 이용된다.
2.2.13 모터위치센서 (motor position sensor)
모터 위치 센서는 ISC(idle speed control) 서보의 플런저 위치를 검출한 신호를 컴퓨터에 보내어 공전 및 냉각수 온도, 에어컨 및 주행 속도 신호를 이용하여 스로틀 밸브를 제어함으로써 공전 속도를 조절한다.
가변 저항으로 센서의 슬라이딩 핀은 플런저 끝 부분에 접촉되어 플런저가 작동할 때 내부 저항이 변화되므로 출력 전압도 변화한다.
이때 변화된 전압이 컴퓨터에 전달되면 모터를 회전시켜 엔진의 회전 속도를 약간 상승시킨다.
2.2.14 인히비터 스위치 (inhibitor switch)
인히비터 스위치는 정속 주행 장치용 스위치를 말한다. 스타터용 스위치와 함께 사용되며.
고정 속도 주행 중 선택 레버를 ‘N’ 위치에 놓으면 전류는 컨트롤 유닛에서 인히비터 스위치와 스타터가 접지로 흐른다.
그 결과 해제 신호가 ECU에 입력되고 고정 속도 주행 모드는 해제된다.
2.2.15 인젝터 (injector)
인젝터는 연료 분사 노즐로서, 연료가 공기와 잘 섞이도록 가는 안개모양의 구조로 되어있다.
ECU로부터 출력된 분사 신호에 의해 연료를 분사하는 솔레노이드 밸브가 내장된 분사 노즐로, 각 실린더의 매니폴드에 1개씩 설치되어 있으며, 연료 공급 파이프와 연결되어 있다.
니들 밸브는 플런저와 일체로 되어 있어, 인젝터 작동 시 플런저와 함께 전개의 위치까지 상승하여 분구를 전개한다.
분사량은 분구의 면적, 연료의 압력이 일정하기 때문에 니들 밸브의 개방 시간 즉 솔레노이드 코일의 통전 시간에 의해 결정된다.
2.2.15.1 콜드 스타트 인젝터 (cold start injector)
기관 시동시 기관의 온도에 따라 흡기다기관 내에 연료를 일정시간 동안 추가적으로 분사시키는 역할로 서모타임 스위치에 의해 제어된다.
2.2.16 퍼지컨트롤 솔레노이드 밸브 (purge control solenoid valve)
퍼지컨트롤 솔레노이드 밸브는 ECU의 신호에 의해 캐니스터에서 기화기(또는 서지 탱크)로 가는 증발 가스를 제어하는 밸브로서, 엔진이 시동되고 특정 조건이 되면 흡기 매니폴드 부압에 의해 밸브가 열려 캐니스터의 증발 연료가 기화기(또는 서지 탱크)로 유입된다.
2.2.17 파워 트랜지스터 (power transistor)
파워 트랜지스터는 흡입 매니폴드에 부착되어 있으며, ECU에 의해 제어되는 단자 1(베이스)과, 점화 코일과 접속된 단자 3(컬렉터), 접지된 단자 2(이미터)로 구성되어 있다.
2.2.17.1 점화코일 (Ignition coil)
점화코일은 스파크플러그의 중심전극과 접지전극 사이에 아주 높은 점화전압이 유도되어 불꽃을 발생시키는데, 이와같은 고전압을 발생(유도)시키는 장치를 말한다.
점화코일은 12V의 배터리 전압을 약 25,000~40,000V 정도까지의 점화전압으로 승압시켜 스파크플러그의 중심전극에서 접지전극으로 또는 접지전극에서 중심전극으로 불꽃이 건너 뛸 수 있게 한다.
점화전압에 영향을 미치는 요소로는 엔진의 압축비, 충진률에 의해 결정되는 실린더압력과 공기비, 혼합기의 유동속도, 와류 그리고 스파크플러그의 간극, 전극형상, 전극재료, 열가 등이 있다. 일반적으로 실린더 압력이 높을수록, 스파크플러그의 간극이 클수록, 공기비가 클수록 점화전압도 더 높아져야 한다.
동시에 점화하는 실린더의 수에 따라 싱글스파크 점화코일과 듀얼스파크 점화코일로 구분한다.
2.2.17.1 싱글 스파크 점화코일 (single spark ignition coil)
싱글 스파크 점화코일은 각 실린더마다 한개씩, 1차코일과 2차코일이 함께 집적된 점화코일이 직접 스파크 플러그에 설치된다. ECU는 크랭크 각 센서와 캠 각 센서가 제공하는 신호에 근거하여 점화 1차 코일을 점화순서에 따라 ON/OFF 시킨다. 점화코일이 실린더별로 장착되어 개별적으로 이를 제어할 수 있으므로 실린더 선택식 노크제어를 적용할 수 있다는 장점이 있다. 즉, 실린더별로 점화시기를 제어할 수 있으므로 노크가 발생하는 실린더만을 선택적으로 점화시기를 지각시킬 수 있다는 것이다.
2.2.17.2 듀얼 스파크 점화코일 (duel spark ignition coil)
듀얼 스파크 점화코일은 1사이클에 각 스파크 플러그에서 불꽃이 2회 발생한다. 따라서 싱글 스파크 점화코일에 비해 스파크 플러그의 열부하가 증대되며 전극의 마모도 빠르다.
1차코일(Primary coil)이 철심(Magnetic core)를 감싸고, 다시 2차 코일(Secondary coil)이 1차 코일을 감싸고 있는 구조이다. 2차코일은 1차코일과 절연되어 있으며 출력단자가 2개이다. 2개의 고전압(High-voltage)단자에는 각각 별개의 스파크플러그와 연결된다. 일부 형식에 따라서는 1개의 스파크 플러그는 점화코일과 직접 연결되고, 나머지는 점화케이블을 통해 연결되는 형식도 있다. 따라서 4기통엔진에는 2개, 6기통엔진에는 3개의 듀얼스파크 점화코일이 필요하다.
1차전류는 ECU가 제어하며, 점화시기를 제어하는 메커니즘은 싱글 스파크 점화코일과 동일하다. 단지 1차전류를 단속하였을 때, 2개의 스파크 플러그에서 동시에 불꽃이 발생된다. 1개의 불꽃은 폭발행정의 실린더에서, 다른 1개의 불꽃은 배기행정의 실린더에서 발생한다. 4기통엔진의 예를들면 1-4실린더, 2-3실린더가 동시에 불꽃을 발생시키게 되는 것이다. 이때, 점화전압은 압축행정의 실린더에서 훨씬 높게 나나타나는데 이유는 스파크플러그의 두 전극 사이에 절연성 가스분자(연료입자)가 훨씬 많이 존재하기 때문이다. 또, 2차코일에 설정된 전류방향으로 인하여 점화불꽃은 1개의 스파크 플러그에서는 중심전극에서 접지전극으로, 다른 1개의 스파크 플러그에서는 이와는 반대로 건너 튀게 된다.
2.2.17.3 4-스파크 점화코일 (four-spark ignition coil)
4-스파크 점화코일은 4기통용이며, 1차코일이 2개, 2차코일은 1개인 구조를 가진다. 2차코일의 양단에는 각각 2개씩의 출력단자가 있으며, 각 출력단자에는 다이오드가 반대로 되어 있다. 이들 출력단자가 4개의 스파크플러그와 연결된다. 다시말해 2개의 듀얼스파크 점화코일이 1개의 하우징 안에 집적된 형식이라고 할 수 있다. 설치와 연결이 간단하다는 장점이 있다.
2.2.18 냉각팬 (Cooling fan)
냉각팬은 라디에이터로 전달된 엔진의 열을 식혀주는 역할을 한다. 고속 주행중에는 주행풍에 의해 라디에이터의 열이 일정 부분 식혀지지만, 저속 주행 중이나 공회전 시에는 주행풍만으로 열의 냉각이 충분하지 않기 때문에 냉각팬을 사용하여 추가적으로 냉각시킨다.
엔진에서 발생한 열은 냉각수(부동액)로 전달되고, 냉각수는 워터펌프에서 서모스탯을 지나 라디에이터로 유입된다. 이 때의 냉각수 온도가 대략 90℃ 정도이다. 외기온도가 20℃에서 시속 140~150km/h 로 주행을 할 경우 주행풍 으로 인해 냉각된 냉각수의 온도는 85℃ 정도가 된다. 이렇게 냉각된 냉각수가 엔진 하부로 유입되며 실린더헤드 부에서 90℃로 되어 다시 라디에이터로 보내진다.
이 때에는 냉각팬이 구동되지 않게 ECU가 제어하게 되고 이를 통해 에너지를 절약할 수 있게 된다. ECU는 냉각수의 온도를 수온센서를 통해 입력받게 된다. 자동차에 따라 다르지만 일반적으로 냉각수 온도가 110~120℃에서 냉각팬은 구동되기 시작하며, 100℃이하가 되면 정지하도록 되어 있다.
2.2.19 ECU (electronic control unit)
엔진 전자제어 장치에서 가장 중요한 요소이다.
애초의 개발 목적은 당시에는 점화시기와 연료분사, 공회전, 한계값 설정 등 엔진의 핵심 기능을 정밀하게 제어하는 것이었다. 그러나 차량과 컴퓨터 성능의 발전과 함께 자동변속기 제어를 비롯해 구동계통, 제동계통, 조향계통 등 차량의 모든 부분을 제어하는 역할까지 하고 있다.
엔진의 회전수와 흡입 공기량, 흡입 압력, 액셀러레이터 개방 정도 등에 맞추어 미리 정해 놓은 점화시기 MAP(Manifold Absolute Pressure) 값과 연료분사 MAP 값 등을 조회하여 수온센서, 산소센서 등을 보정하고 인젝터의 개폐율을 조정한다. 이렇게 하여 연료의 분사량과 점화시기를 결정한다. 엔진이 망가지지 않도록 각 항목별 수치에 한계값이 설정되어 있다.
2.2.20 컨트롤 릴레이 (control relay)
자동차의 컨트롤 릴레이는 엔진의 ECU부분에 장착되어 연료모터의 구동과 연료모터의 작동 차단하는 역할을 한다.
엔진이 회전하고 있다는 신호를 크랭크 각 센서로부터 받은 ECU는 연료모터를 구동, 유지 시키기 위해 컨트롤릴레이를 작동 시킨다.엔진 ECU의 신호를 받은 컨트롤 릴레이는 연료모터에 작동 전원을 공급한다.
시동을 껐을 때나 사고가나서 시동이 강제적으로 꺼졌을 때. ECU는 컨트롤 릴레이를 제어하며 연료가 계속해서 펌핑 되는 것을 차단한다.
2.2.21 스텝 모터 (step moter)
스텝모터는 모터 구동방식의 하나로써 한 방향으로 고속회전을 하는 모터와는 달리 전류의
단속으로 양방향으로 1스텝씩 움직일 수 있는 모터를 말한다.
자동차에서는 주로 엔진 공회전시 실린더 내로 공기를 알맞게 들여보내주는데 쓰인다.
스텝모터는 엔진 ECU가 단속하며 에어컨을 켤 때나 전기부하가 걸릴 때, 그리고 오토 미션 차량인 경우엔 미션부하가 걸릴 때 공회전속도를 조정하기 위해 엔진ECU에서 신호를 보내 스텝모터를 작동 시킨다.
장착위치는 흡기 서지탱크의 공기 흡입부에 있는 스로틀바디에 장착되어 있는 차량도 있으며,바이패스 방식으로 서지탱크와 에어인테이크 호스 사이에 장착 되어지는 차량도 있다.
2.2.22 증발가스 제어장치 (evaporation gas control system)
증발가스 제어장치는 휘발성이 높은 자동차용 가솔린이 탱크나 기화기에서 증발하여 캐니스터에 일시적으로 저장되었다가 특정 조건이 되면 흡기 매니폴드로 보내 연소되는 장치로서, 이 장치는 캐니스터, 퍼지 컨트롤 솔레노이드 밸브(탱크 브리더 밸브) 등으로 구성되어 있다.
2.2.22.1 활성탄 캐니스터 (charcoal canister)
캐니스터(canister) 내에는 활성탄 입자들이 가득 들어있다. 기관이 정지한 후에 연료탱크와 혼합기 형성기구에서 발생하는 연료의 증발가스는 가는 호스(hose)를 통해 모두 캐니스터로 유입된다. 캐니스터에 유입된 증발가스는 곧바로 활성탄 입자의 표면에 흡착된다.
기관작동 중 ECU가 셧-오프(shut-off)밸브의 대기 유입구와 재생밸브(regenerative valve)의 소기공을 동시에 열면, 활성탄에 흡착된 상태인 증발가스는 다시 활성탄으로부터 분리되어 흡기다기관으로 유입된다. 따라서 증발가스는 곧바로 대기 중으로 방출되지 않고 반드시 연소과정을 거치게 된다.
2.2.22.2 재생 밸브와 셧-오프 밸브(regenerative valve and shut-off valve)
캐니스터에 포집된 증발가스를 제어하는 밸브들로서 공전 시와 난기운전 중에는 작동되지 않는다. 공전 시와 난기운전 중을 제외하고는 ECU의 명령에 따라 동시에 ON/OFF 제어된다. 그러나 OBD에서 연료탱크 시스템의 누설여부를 감시할 때는 공전 시에 재생밸브만 연다. 그러면 흡기다기관의 압력이 전체 시스템에 작용하게 된다. 이때 연료탱크에 설치된 압력센서가 압력변화를 감시하고, 이 압력변화로부터 연료탱크시스템의 누설여부를 판정한다.
2.2.23 블로 바이가스 제어장치 (blowby gas control system)
블로바이가스 제어장치는 엔진오일이 분리된 블로 바이가스를 계속해서 흡기다기관으로 유도하고, 동시에 기관내부(크랭크실 등)에 고압이 걸리지 않도록 하여, 오일 소비를 감소시키는 역할을 한다.
GDI–기관이나 과급디젤기관에서는 블로 바이가스에 포함된 오일 성분 및 고형 미립자(PM)들이 과급기에, 분사밸브에, 과급공기 냉각기에, 그리고 경우에 따라서는 뒤에 접속된 매연필터에 악영향을 미치는 것으로 알려져 있다.
2.2.23.1 크랭크케이스 강제 환기장치(positive crankcase ventilation system)
크랭크케이스 강제 환기장치에서는 공기여과기를 통과한 새로운 공기가 지속적으로 또는 부하에 따라 제어되어 크랭크케이스로 유입된다. 이 새로운 공기는 블로바이가스와 미세한 오일 입자들이 혼합된 가스에 추가로 혼합된다. 시스템제어는 조정된 스로틀과 밸브를 통해 이루어진다. 오일분리는 기존의 시스템에서와 동일한 방법으로 이루어진다. 블로바이가스는 흡기계로 유도되어 재 연소된다.
블라바이가스에 포함된 수증기와 연료증기는 유입되는 새로운 공기에 흡수되므로, 결과적으로 응축 가능한 증기(연료 및 수분)의 농도가 낮아져, 아주 낮은 온도에서도 전혀 응축되지 않거나, 또는 최소한으로 극히 일부만이 크랭크케이스 내에서 응축된다. 외기온도가 아주 낮고, 주위공기가 건조하면 특히 효과가 크다. 응축액에 포함된 수분이 추위에 의해 빙결될 경우, 최악의 경우에는 윤활회로를 차단하여 기관을 완전히 파손시킬 수 있다. 결빙은 또 크랭크케이스 환기통로를 부분적으로 막아 크랭크케이스의 압력상승을 유발할 수 있다. 크랭크케이스의 압력이 상승하면 유면게이지, 베어링 씰, 밸브커버 개스킷 등을 통해 오일이 누설되게 된다.
그리고 여과되지 않은 블로바이가스가 PCV 라인을 통해 역류하는 것을 방지하기 위해 시스템에 PCV밸브(체크밸브)를 설치한다.
PCV–시스템의 단점으로는 경우에 따라서 산화에 의해 오일의 노화가 촉진되고 흑색 슬러지(black sludge:Schwarzschlamm)의 생성도 촉진된다는 점이다. 유입되는 새로운 공기에 포함된 산소는 오일의 산화를, 잔류물은 오일 찌꺼기의 생성을 촉진시킨다.
2.2.23.2 부압 제어식 크랭크케이스환기장치(vacuum controlled crankcase ventilation system)
부압 제어식 크랭크케이스 환기장치에서 블로바이가스는 오일분리기로부터 부압제한밸브를 거쳐 스로틀밸브 후방의 흡기다기관으로 유입된다. 기존의 시스템과 비교하여 오일분리기와 스로틀밸브 전방의 흡기다기관 사이의 연결라인, 그리고 스로틀밸브 후방의 흡기시스템과 기관 사이의 스로틀(throttle) 라인도 생략되었다(그림 10-9(a), 그림 10-9(b)와 그림 10-10을 비교해 볼 것).
부압제한밸브는 스프링 부하된 다이어프램밸브인데, 조정된 바이패스 통로를 갖추고 있다. 이 밸브는 기관의 거의 모든 부하 상태에서 기관 내부의 부압을 허용 최댓값 이하로 제어한다. 기관내부의 부압이 지나치게 높아도, 기존의 크랭크케이스 환기장치에서의 부정적인 현상들이 나타날 수 있다.
이 시스템을 이용하여, 기관의 전체 작동범위에 걸쳐 크랭크케이스의 부압 수준을 일정한 범위로 유지할 수 있다. 기존의 크랭크케이스 환기장치에 비해 부품수가 적으며 호스 내부에서의 결빙 위험도 낮다. 블로바이가스를 스로틀밸브 후방의 흡기다기관에 유입되게 함으로서 공기질량계량기와 공전 액추에이터의 오염도 방지한다.
이론적으로는 부압제한밸브의 다이어프램에 고장이 발생할 수 있다는 점이 단점이다. 그러나 실제로 그러한 경우는 보고되지 않고 있다.
2.2.24 촉매기 시스템(catalysator system)
촉매(catalyst)란 그 자신은 변화하지 않으면서 다른 물질의 화학반응을 촉진시켜 주는 물질을 말한다. 자동차에서 촉매기란 배기가스 중의 유해물질을 산화(oxidation) 또는 환원(reduction)반응을 통해 무해한 물질로 변환시켜 주는 장치를 말한다.
촉매기에서의 화학반응은 NOx는 먼저 환원 반응하여 N2와 O2로 분리되고, 분리된 O2는 다시 CO와 반응하여 CO2가 된다. 그리고 CO와 HC는 산화 반응하여 CO2와 H2O로 변환된다.
촉매기 시스템은 세가지로 분류할 수 있는데 1상 산화촉매기(single-bed oxidation catalytic converter)와 2상 촉매기(dual-bed catalytic converter), 1상 3원촉매기(single-bed 3-way catalytic converter:Dreiwege Katalysator)로 나눌 수 있다.
2.2.24.1 1상 산화촉매기(single-bed oxidation catalytic converter)
1상 산화촉매기는 공기과잉상태에서 CO와 HC를 H2O와 CO2로 산화 즉, 연소시킨다. 질소와 결합된 산소는 산화촉매기에서는 반응하지 않는다.
산화에 필요한 산소를 희박혼합비(λ>1)를 통해 공급하거나, 소위 2차공기(secondary air)를 촉매기 전방에 분사하는 방법이 주로 사용된다.
2.2.24.2 2상(床) 촉매기(dual-bed catalytic converter)
초기의 2상 촉매기는 환원촉매기와 산화촉매기가 연이어 설치된 형식이 대부분이었으며, 2차공기는 두 촉매기 사이에 공급하였다. 앞 촉매기(환원촉매기)에서는 NOx가 환원반응하여 N2와 O2로 분리되고, 뒤 촉매기(산화촉매기)에서는 HC와 CO가 산화반응하여 H2O와 CO2로 변환된다. 농후혼합기가 공급될 때에는 공기부족 상태이므로 질소산화물이 환원촉매기에서 환원반응할 때 암모니아(NH3)가 생성될 수 있다. 이때 생성된 암모니아의 일부는 2차공기가 공급되면 다시 질소산화물로 변환되게 된다.
최근에는 앞에 3원촉매기, 뒤에 De-NOx촉매기를 설치한 형식이 GDI–기관에 도입되고 있다
2.2.24.3 1상 3원촉매기(single-bed 3-way catalytic converter:Dreiwege Katalysator)
1상 3원촉매기는 1개의 촉매기에서 3종류의 유해물질(HC, CO, NOx)이 동시에 산화 또는 환원반응한다는 의미를 가지고 있다. 3원촉매기에서의 화학반응은 공기비가 이론혼합비(λ=1)에 가까워야만 정화율이 높다. 그 이유는 다음과 같다.
환원반응에 의해서 NOx로부터 분리된 산소의 양은 배기가스 중의 CO와 HC를 모두 산화반응시킬 수 있을 정도로 충분해야 한다. 따라서 공기비가 이론혼합비보다 낮으면(λ<0.99), 산소부족이 되어 CO와 HC의 발생률이 높아진다. 반대로 공기비가 이론혼합비보다 높으면(λ>1.00), 산소과잉이 되어 CO와 HC의 발생률은 낮아지지만 NOx의 발생률은 증가한다. 따라서 3원촉매기는 공기비센서와 함께 사용하는 것이 효과적이다.
공기비를 제어하지 않고 3원촉매기만을 사용할 경우에는 유해물질의 약 60% 정도를 저감시킬 수 있을 뿐이다. 그러나 공기비제어 및 공기비 감시시스템이 설치된 경우, 촉매기에서의 정화율은 약 94~98% 정도에 이른다.
자율주행차, 사람보다 안전한 운전 비밀은 ‘센서 3형제’에 있다
인간의 외부 자극은 오감(시각·청각·후각·미각·촉각)으로부터 수용된다. 이 자극은 전기 신호를 통해 중추신경계로 전달되고, 이를 통해 사고하고 행동한다. 자율주행차는 전통적인 차량과 달리 인간처럼 사고하고 스스로 운행해야 한다. 자율주행차의 운행 원리도 인간이나 동물의 사고 과정과 유사하다. 인간이 신경세포(뉴런)로부터 감각을 느끼듯, 자동차도 기본적으로 탑재된 센서들이 주변 환경 요소를 인식한다. 차량 내 인공지능(AI) 컴퓨터(PC)는 센서에서 수집한 정보로 차량을 제어한다. 이 제어기가 자동차의 각 부품에 명령을 내리면, 마치 인간이 두 발로 움직이듯 자동차도 스스로 움직인다.
이처럼 생각과 움직임의 근간은 감각기관을 통해 수집되는 정보다. 인간이 사고하고 행위하는 것도 두 눈으로 활자를 읽고, 귀로 음성을 듣기 때문이다. 때문에 정확한 정보 수집은 매우 중요하다. 수집된 정보가 부정확하면 이후 중추신경계의 판단과 이에 따른 움직임도 잘못될 가능성이 크기 때문이다. 자율주행차가 인간의 도움 없이 스스로 안전하게 운행하기 위해서 고도화된 감지 능력이 필요한 이유다.
자율주행차 핵심 센서…카메라·레이더·라이다
자율주행차의 주변 환경 인식은 크게 카메라와 레이더, 라이다 등을 포함한 3개의 센서에서 시작된다. 인간의 눈, 코, 입, 귀의 역할이 다른 것처럼 각 센서의 전문 분야도 다르다. 우선 카메라 센서는 사람과 사물, 차량 등으로 분류하면서 주변 물체 식별에 사용된다. 다만 어두운 공간이나 악천후 상황에선 확실한 사물 식별이 어렵다. 카메라를 차선 인식 용도로만 이용했던 과거와는 달라진 모습이다. 이스라엘 카메라 알고리즘 업체인 ‘모빌아이’ 정도만 앞차와의 거리나 도달 시간 등을 이용해 운전자보조장치(DAS)를 상용화했다. 최근 들어선 테슬라와 현대모비스 등이 연석이나 자갈, 잔디를 인식하는 카메라 기술 개발에 성공해 양산 중이다. 평면에만 국한됐던 인식 기능이 돌출된 구조물 파악까지 가능해진 셈이다.
원래 군사목적으로 개발됐던 레이더의 경우엔 전자기파를 발사하고 반사돼 돌아오는 신호를 기반으로 주변 사물과의 거리, 속도, 방향 등의 정보를 추출하는 센서다. 또 날씨, 시간과 관계없이 제 성능을 발휘한다. 레이더는 주파수에 따라 단거리부터 중거리, 장거리를 모두 감지할 수 있다는 점에서 현재도 긴급자동제동장치, 스마트 크루즈 컨트롤 등 다양한 첨단운전자보조시스템(ADAS) 기술에 적용되고 있다.
주파수는 긴 파장의 저주파일수록 상대적으로 동일한 출력의 전파를 쏘아도 도달 거리가 길어지는 반면 정확도는 떨어진다. 이런 특성으로 장거리 레이더 센서는 저주파인 77기가헤르츠(㎓) 대역을 사용한다. 보다 명확한 정보가 요구되는 단거리 레이더 센서의 대역폭은 79㎓ 대역을 이용한다. 장거리 레이더는 150~200m 이상까지 확인되지만 화각이 40도 안팎이다. 단거리 레이더의 경우엔 100m 이내 거리를 감지하지만 화각은 100도 이상이다.
라이다는 레이저(빛)를 물체와 주고받으며 3차원 지도를 만들어낸다. 주로 905나노미터(nm)의 짧은 파장을 이용해 레이더보다 공간 분해능력이 훨씬 정밀하다. 또 자체 광원으로 빛이 부족환 환경에서도 성능에 영향을 덜 받는다. 때문에 카메라, 레이더가 감지하지 못하는 환경에서도 활용할 수 있다. 최근에는 출력을 1,550nm까지 높여 훨씬 더 넓은 공간을 인식할 수 있는 기술도 개발됐다. 이는 사람 눈에 흡수되지 않고, 태양광의 간섭현상도 적어 안정성이 뛰어나다.
작동 방식이 사람의 눈과 유사한 라이다는 ‘자율주행차의 눈’으로 불린다. 사람은 왼쪽 눈과 오른쪽 눈 사이의 거리, 왼쪽 눈에서 보이는 물체와 오른쪽 눈에서 보이는 물체의 거리를 계산해서 실제 대상 물체와의 거리를 파악한다. 라이다는 초당 수십 번의 레이저를 주변 사물들과 주고받으면서, 정밀하게 거리 정보를 파악할 수 있다. 이는 자율주행 시스템의 신뢰를 높이는 데 중요한 역할을 한다. 다만 고가인 라이다의 경우, 빛을 이용하는 만큼 악천후 시 정확도가 떨어진다.
자율주행 안전성 대결…”카메라 vs 센서퓨전”
이처럼 자율주행차의 안전하고 정확한 운행엔 각 감각기관들의 특징이 적절하게 발휘돼야 한다. 레이더만으로는 물체의 정확한 식별이 불가하고, 카메라는 혼자서 원근감을 정확히 판별하기에는 아직 한계가 있기 때문에 각자의 부품들이 제 역할에 맞게 기능해야 한다. 이런 다양한 센싱 기술의 연구와 개발은 자동차 업계의 미래 경쟁력 확보에선 필요충분조건이다.
자동차 업계는 이런 기술력을 실제 주행에 완벽히 녹여내기 위해 소프트웨어(SW) 개발에도 주력한다. ‘센서 퓨전’은 각 센서에서 인식된 정보를 하나로 결합, 자율주행이 가능하도록 한 기술이다. 카메라, 레이더, 라이다 등 각 기술의 장·단점을 서로 보완하는 것이다. 최근에는 AI 기술까지 더해지면서 자동차 시스템이 사람 뇌처럼 각 센싱 정보를 융합해 차량 주행 알고리즘까지 설계한다.
일부 업체들은 가격적인 측면에서 센서 퓨전 기술 대신, 하나의 센서만 이용한 자율주행 기술을 개발하고 있다. 미국의 전기차 업체 테슬라가 대표적이다. 일론 머스크 테슬라 최고경영자(CEO)는 라이다의 가격이 비싸고, 소비전력이 크다는 이유로 카메라 센서만 이용한 자율주행차를 만들겠다고 선언했다. 8대의 카메라가 입체적으로 촬영하면 물체의 형태, 거리를 측정해 자율주행이 가능하다는 것. 오히려 레이더는 왜곡된 데이터가 많아 정밀도를 떨어뜨린다는 게 머스크 CEO의 판단이다.
하지만 여전히 대부분 자율주행차는 다양한 센서를 사용하고 있다. 자율주행 선두주자인 구글의 웨이모는 라이다를 중심으로 레이더, 카메라를 함께 사용한다. 볼보는 내년 출시할 차세대 전기차에 카메라, 레이더와 함께 라이다 센서 업체인 루미나 제품을 장착한다. 아우디는 2017년 최초로 A8에 센서업체 발레오의 라이다를 사용했다. 현대자동차도 내년 출시할 제네시스 G90에 2개의 라이다를 탑재할 예정이다.
류종은 기자 [email protected]
0 0 공유 카카오
페이스북
트위터
이메일
URL 기사저장
국내 유일 자동차 변위센서 생산기업… “글로벌 트루윈 도약할 것”
㈜트루윈 대전 본사 전경. 이곳은 약 5만9504㎡(약 1만8000평) 규모로 축구장 8배에 달한다.
핵심원천기술 확보에 주력
크게보기 ㈜트루윈이 생산하는 제품
시장분석과 대비 통해 미래차 시장 기대감 커져
기술 수준도 글로벌 기업과 어깨 나란히
열영상 카메라 ‘써모비’ 출시
㈜트루윈의 열화상 카메라 ‘써모비’.
한우물 판 우직한 경영… “열의와 정성이 경쟁력”
㈜트루윈의 남용현 대표.
최근 자율주행차 등 미래 자동차 산업 비중이 높아지면서 차량 센싱 기술의 가치도 함께 올라가고 있다. 차량 센싱은 다양한 측정 대상으로부터 정보를 확인해 전기신호로 바꾸는 작업을 일컫는데 최근 들어서 차량에 필요한 정보 종류 등이 점차 다양화하고 있다. 또 차량 안전에 대한 요구가 커지면서 센서를 통해서 안전도를 높이려는 시도도 늘어나고 있다. 멀리 미래차까지 갈 필요가 없이 현재도 센싱 기술이 광범위하게 활용되고 있다. 해외선 이미 센서 산업이 전장 주요 산업으로 각광받는 분위기다.국내서도 많은 기업들이 전장 센서 분야에 도전했지만 대부분은 높은 진입장벽 탓에 포기했다. 개발비용이 적지 않고 사업화 속도가 더디기 때문이다.2014년 코스닥에 상장된 ㈜트루윈은 국내에서는 유일하게 변위 센서 원천기술을 확보했고 이를 발판 삼아 지속적으로 센싱 기술을 확장해나가는 기업이어서 주목된다.이는 무엇보다 자동차의 전장화에 따른 자동차 전장 제어의 핵심기술인 반도체(Asic)의 설계기술을 보유하고 있다는 점에서 차별성이 두드러진다. 이 밖에 적외선 열화상 센서 및 카메라 모듈 관련 핵심 원천기술을 확보하는 데 성공했다. 최근 차량 안전성과 관련해 주목받는 센싱 기술이다. 미래차 성장과 더불어 성장할 기업으로 꼽힌다.대전에 위치한 트루윈은 자동차 전장 핵심 부품인 액셀러레이터 페달 센서(APS), 스톱램프 스위치(SLS) 등을 생산하는 기업으로 잘 알려져 있다. 전장 센서 부문은 정밀성과 안전성 모두 높은 기준을 요구하기에 진입장벽이 높게 형성돼 있지만 트루윈은 사업 초창기부터 막대한 연구개발(R&D) 투자를 통해서 기술을 확보해 나갔고 진입장벽이 높았던 센서 기술을 차츰 국산화하는 성과를 거둘 수 있었다. 트루윈은 해외에서 수입한 센서칩을 가공해 대기업에 납품하던 국내 관행을 깨뜨리고 국산차에 들어가는 국산 센서 기술을 실현해나가고 있다.회사 기술 성장의 핵심 발판은 2006년 설립 당시부터 R&D를 주도한 기업부설연구소가 꼽힌다. 부설연구소를 통해 근접센서의 원리를 이용한 차량용 스위치, 미등 및 정지등을 겸하는 정지스위치센서와 전자식 스탑램프 스위치 등 자동차 주요 부품들을 연이어 개발하는 데 성공하면서 일약 국내 전장 센서 부문에서 주목할 기업으로 떠올랐다. 현재도 창업 초기에 개발된 센서들은 하나하나 자동차 산업을 비롯해 신산업분야 공급망에 필수적인 역할을 하고 있다.높은 진입장벽에도 불구하고 트루윈이 전장 센서 부분을 주목하고 이 분야에 뛰어든 이유가 있다. 트루윈 남용현 대표는 엔지니어 출신으로 삼성 SDI연구소 선임연구원과 동희산업 연구소장을 지냈다. 그는 “여러 완성차 업체들이 센서 결함으로 고민할 때 이를 기술적으로 해결해 준 경험이 있다”고 회고했다. 그때 차량 센서 기술의 중요성을 체감하고 미래차 시장 성장과 더불어 성장할 수 있는 시장이라는 점을 직감했다. 한 차례 사업 경험을 거쳐 2006년 고향인 대전에 자리 잡고 처음부터 기술 개발에 매진했다. 지역을 대표하는 기술혁신 기업으로 자리 잡으며 꾸준한 제품 개발과 국산화 성공으로 트루윈의 비전은 국내를 넘어 세계를 향하고 있다.남 대표는 공학도 출신으로 분석과 계산을 통해 답을 얻고자 노력한다. 그는 “센서 기술이 미래차 시장에서 특히 중요해질 것이라는 예상은 적중했고 최근 전기차의 수요 증가와 해당 기술에 대한 관심이 높아지면서 더욱 빛을 발하고 있다”고 전했다.트루윈은 전기차용 부품 공급에 잇달아 성공하며 경쟁력을 입증하고 있다. 지난달 현대차 아이오닉5에 ‘SLS 센서’를 독점 공급하는 성과를 거둔 게 대표적이다. ‘SLS’는 브레이크 페달 움직임을 감지해 차량 브레이크 램프 점등 신호를 출력하는 비접촉식 스위치로 내구성이 뛰어나 기존 기계식 스위치 대비 물리적 마모가 적으며 접점 불량도 없는 것이 장점이다. 앞서 지난해 12월에는 중국의 전기차업체 ‘니오’에 전기차용 센서인 ‘BPS(브레이크 페달 센서)’ 공급 계약도 체결했다. 2022년 상반기 내 6만 개 초도물량을 공급할 계획이다. 남 대표는 “꾸준히 성장하는 전기차 시장에 맞춰 제품 수출량이 큰 폭으로 늘어날 것”이라고 내다봤다.트루윈은 지속적인 사업다각화 전략을 통한 수익성 개선으로 2020년 매출액 377억 원을 달성하며 전년 대비 27% 성장했다. 영업이익, 당기순이익도 흑자전환에 성공하는 등 최근 성장세가 두드러진다.국내 전장 센서 분야서 독보적인 위치를 차지하게 된 비결을 묻는 질문에 트루윈 남 대표는 “자동차 센서시장 특성상 원천기술만이 살 길이라는 것을 알고 기술개발에 총력을 기울인 결과”라고 설명했다. 아울러 “처음 사업을 시작할 때만 하더라도 시장서 요구하는 높은 기술 수준은 진입장벽으로 작용했으나 현재는 후발주자와의 격차를 벌리는 장점이 됐다”고 덧붙였다.트루윈이 선보이고 있는 많은 센서 부품 중에서도 압력센서인 ‘IPS’와 변위센서인 ‘EPS’, 열상센서인 ‘IR센서’가 최근 크게 주목받고 있다. ‘IPS’는 금속이나 세라믹에 가해지는 유압 또는 대기 압력의 미세 변위를 이용해 압력을 측정하는 센서로 각종 압력에 반응하는 미세단위의 기계적 변위까지도 측정하는 게 기술력이다. 기존 기술과 차별화된 원천기술을 확보하면서 현재 트루윈이 확보한 관련 특허만 약 20건에 이른다.‘EPS’에는 금속 물체의 접근 유무를 판단해 각종 위치 정보를 측정하는 기술이 담겨 있다. 자석 없이 금속 자체의 유무를 감지하는 원천기술을 확보했는데 관련 특허도 약 40건에 이른다.‘IR센서’는 생체 또는 각종 기계로부터 발생하는 열발생 정보를 측정하는 센서로 트루윈은 반도체 표준 공정을 이용해 기존 가격 대비 20% 수준 내에서 관련 제품 생산에 성공했다. 관련 특허가 약 10건에 이르는데 활용 폭이 넓어 방범이나 의료 자율주행 등에서도 쓰일 수 있을 것으로 보인다. 2025년에는 관련시장 규모가 약 10조 원에 달할 것으로 예상된다. 스마트폰에 접목할 경우 규모는 25조 원까지 커질 것으로 내다보고 있다.2월 한화시스템과 열상 모듈 및 제품 사업을 위한 전략적 업무협약(MOU)을 체결하기도 했다. ‘IR센서’ 및 열상엔진모듈 양산에도 능력을 갖춘 트루윈은 한화시스템이 자체 개발한 지능형 열상엔진모듈 ‘퀀텀레드’를 주문자상표부착 방식(OEM)으로 독점 생산해 공급한다.두 회사는 퀀텀레드를 활용해 자율주행 자동차용 열상카메라 나이트비전에 대해 공동연구를 추진할 계획이다. 사람이나 사물 온도를 근거리에서 정밀 측정하는 소형 및 저가 지능형 열상엔진모듈 개발도 논의 중이다.한편 트루윈의 센서 기술이 최근 급성장해 자동차 센서 명가인 독일 보쉬, 일본 덴소 등 글로벌 기업들과 경쟁할 만한 기술력을 갖췄다는 평가를 받고 있다. 현재 신종 코로나바이러스 감염증(코로나19)으로 전 세계 전시회 등이 올스톱 돼 트루윈 기술을 선보일 수 있는 공간이 줄어든 가운데서도 다수 글로벌 기업들이 협업을 제안해 기대감이 크다.트루윈의 자체 개발 역량과 기술력이 담긴 열영상 카메라인 ‘써모비’도 최근 주목받는 제품이다. 이 회사는 코로나19로 급증하고 있는 열영상 카메라 수요를 충족하기 위해 지난해 3월 열영상 카메라 써모비를 시장에 선보였다. 코로나19 유행 초창기에 출시되면서 시장 형성기에 일찍부터 두각을 나타낸 제품이다.써모비는 생체 온도인 32도에서 42도 사이의 온도 구간에서 0.3도 내의 정밀성을 갖는 절대온도 측정용 열영상 카메라다. 이미 양산 체제를 구축한 해상도 80×60의 적외선 열영상 센서가 탑재돼 직접 인체 및 동물의 온도를 정밀히 측정할 수 있다. 트루윈은 NNFC(나노종합기술원)와 공동 개발을 마친 CMOS 전용 공정을 활용해 원가를 절감한 대량생산 기술을 확보했다.지난해 11월에는 후속 제품인 ‘써모비_T’를 출시했다. 태블릿 PC와 일체형으로 개발돼 쉽고 편리한 이용이 가능하다. CIS(CMOS 이미지 센서) 카메라와도 연동돼 기존보다 더 정밀하게 온도 측정을 할 수 있으며 원격제어를 통해 누구나 손쉽게 유지 보수가 가능하다는 것이 장점이다.남 대표는 “써모비는 현재 정부기관 및 관공서 공급을 위한 조달청의 업체등록을 마쳤을 뿐 아니라 전국의 일반 소매 및 기업 간 거래(B2B) 판매 등에서 두루 영역을 넓혀 나가고 있다”고 말했다. 아울러 “대전 지자체와 지역 내 소상공인에게 합리적인 납품을 위한 방법이 논의되고 있다”며 “지역경제가 다시 살아나길 바란다”고 밝혔다.정상연 기자 [email protected]“자동차 센서와 시스템 반도체 사업영역은 바이오산업과 유사합니다. 기술개발에 3∼5년 투자하고 임상을 하고 시장에 성공적인 안착을 하면 롱런을 하는 방식이죠.”엔지니어 출신인 트루윈 남용현 대표는 “전장 센서 사업도 원천기술을 다루는 사업”이라며 “바이오산업과 유사점이 많다”고 말했다. 비록 바로 성과가 나지 않더라도 우직하게 투자와 연구를 밀어붙여야 훗날 큰 성과를 낼 수 있다는 것이다. 남 대표는 한우물만 판 덕분에 전장 센서 국산화를 이뤄낼 수 있다고 말했다.트루윈의 장인정신은 업계에선 정평이 나있다. 고객사가 원하는 내구성 테스트가 1000만 번 정도여도 12배인 1억2000만 번 테스트를 할 정도다. 남 대표는 “센서의 핵심은 인식률과 내구성인데 자동차에 들어가는 만큼 단 한 건의 불량도 있어선 안 된다는 게 철칙이자 소신”이라고 말했다. 트루윈 제품에 대한 리콜 사태는 창립 이후 지금까지 단 한 차례도 없다.현재 트루윈은 130여 명의 임직원이 대전 본사에서 근무 중인데 매출의 10% 이상을 이 회사의 연구개발에 투자할 정도로 기술에 대한 투자를 아끼지 않고 있다.남 대표는 ‘열의와 정성’이라는 사훈을 내걸고 모든 일에 솔선수범한다. 직원들에게도 애사심이나 성과를 강요하지 않는다. 그 대신 자신의 능력을 최대한 살리면서 회사와 함께 성장하라고 말한다. 장인정신은 강요가 아니라 동기부여를 통해서 이뤄진다는 점을 남 대표는 스스로 잘 알기 때문이다. 이러한 장인정신을 바탕으로 트루윈은 2006년 창업 이래 국내 전장 센서 부문 국가대표 기업으로 성장했다.남 대표는 2014년에는 해외에 의존하던 센서 기술 국산화 성과를 바탕으로 코스닥에도 상장했다. 그는 “리스크를 안고 한우물을 파는 것은 어리석지만 주어진 환경과 기술력, 인력, 시장을 예측하는 안목 등을 기반으로 집중해 나간다면 국내 많은 벤처기업들이 유니콘(시장가치 1조 원 이상 비상장 벤처기업)이 될 수 있을 것”이라고 말했다.
키워드에 대한 정보 자동차 센서
다음은 Bing에서 자동차 센서 주제에 대한 검색 결과입니다. 필요한 경우 더 읽을 수 있습니다.
이 기사는 인터넷의 다양한 출처에서 편집되었습니다. 이 기사가 유용했기를 바랍니다. 이 기사가 유용하다고 생각되면 공유하십시오. 매우 감사합니다!
사람들이 주제에 대해 자주 검색하는 키워드 108.자주나오는 센서의 역활 / 자동차정비기능사실기
- #videoshowapp made with @videoshowapp
108.자주나오는 #센서의 #역활 #/ #자동차정비기능사실기
YouTube에서 자동차 센서 주제의 다른 동영상 보기
주제에 대한 기사를 시청해 주셔서 감사합니다 108.자주나오는 센서의 역활 / 자동차정비기능사실기 | 자동차 센서, 이 기사가 유용하다고 생각되면 공유하십시오, 매우 감사합니다.